การวิเคราะห์โดยละเอียดของแพทช์ SMT และ THT ผ่านปลั๊กรู PCBA สามกระบวนการเคลือบสีต่อต้านและเทคโนโลยีที่สำคัญ!
เมื่อขนาดของส่วนประกอบ PCBA มีขนาดเล็กลง ความหนาแน่นก็จะสูงขึ้นเรื่อยๆ ความสูงที่รองรับระหว่างอุปกรณ์และอุปกรณ์ (ระยะห่างระหว่าง PCB และระยะห่างจากพื้นดิน) ก็มีขนาดเล็กลงเรื่อยๆ และอิทธิพลของปัจจัยด้านสิ่งแวดล้อมที่มีต่อ PCBA ก็เพิ่มขึ้นเช่นกัน ดังนั้นเราจึงนำเสนอข้อกำหนดที่สูงขึ้นเกี่ยวกับความน่าเชื่อถือของ PCBA ของผลิตภัณฑ์อิเล็กทรอนิกส์
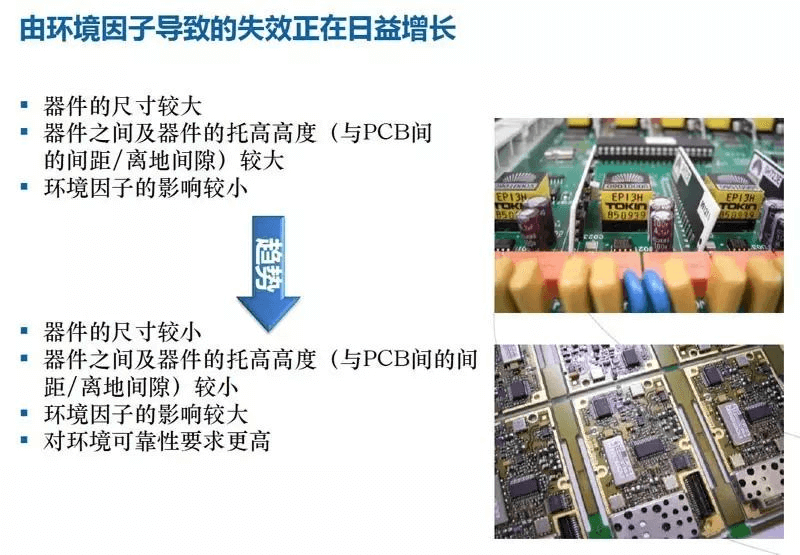
1.ปัจจัยด้านสิ่งแวดล้อมและผลกระทบ
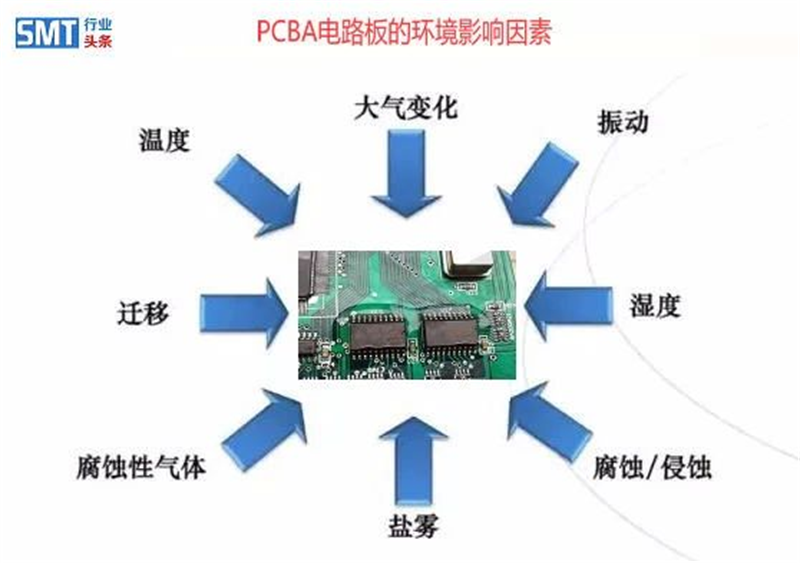
ปัจจัยด้านสิ่งแวดล้อมทั่วไป เช่น ความชื้น ฝุ่น สเปรย์เกลือ เชื้อรา ฯลฯ อาจทำให้เกิดปัญหาความล้มเหลวต่างๆ ของ PCBA
ความชื้น
ส่วนประกอบ PCB อิเล็กทรอนิกส์เกือบทั้งหมดในสภาพแวดล้อมภายนอกมีความเสี่ยงต่อการกัดกร่อน โดยน้ำเป็นตัวกลางที่สำคัญที่สุดในการกัดกร่อน โมเลกุลของน้ำมีขนาดเล็กพอที่จะเจาะช่องว่างโมเลกุลแบบตาข่ายของวัสดุโพลีเมอร์บางชนิดและเข้าสู่ภายในหรือเข้าถึงโลหะที่อยู่ด้านล่างผ่านรูเข็มของสารเคลือบเพื่อทำให้เกิดการกัดกร่อน เมื่อบรรยากาศมีความชื้นถึงระดับหนึ่ง อาจทำให้เกิดการโยกย้ายทางเคมีไฟฟ้าของ PCB กระแสรั่วไหล และการบิดเบือนของสัญญาณในวงจรความถี่สูงได้
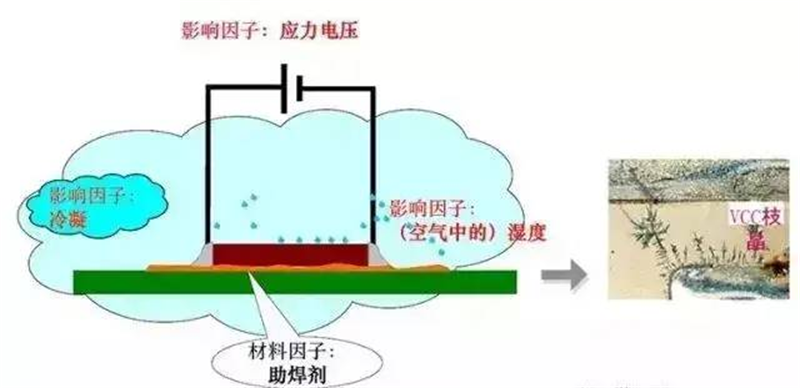
ไอ/ความชื้น + สารปนเปื้อนไอออนิก (เกลือ สารออกฤทธิ์ของฟลักซ์) = อิเล็กโทรไลต์ที่เป็นสื่อกระแสไฟฟ้า + แรงดันความเครียด = การเคลื่อนย้ายทางเคมีไฟฟ้า
เมื่อ RH ในบรรยากาศถึง 80% จะมีฟิล์มน้ำที่มีความหนา 5~20 โมเลกุล และโมเลกุลทุกชนิดสามารถเคลื่อนที่ได้อย่างอิสระ เมื่อมีคาร์บอน ปฏิกิริยาเคมีไฟฟ้าอาจเกิดขึ้นได้
เมื่อ RH ถึง 60% ชั้นผิวของอุปกรณ์จะสร้างฟิล์มน้ำหนา 2~4 โมเลกุลของน้ำ เมื่อมีสารมลพิษละลายก็จะเกิดปฏิกิริยาทางเคมี
เมื่อ RH < 20% ในบรรยากาศ ปรากฏการณ์การกัดกร่อนเกือบทั้งหมดจะหยุดลง
ดังนั้นการป้องกันความชื้นจึงเป็นส่วนสำคัญในการปกป้องผลิตภัณฑ์
สำหรับอุปกรณ์อิเล็กทรอนิกส์ ความชื้นมีสามรูปแบบ ได้แก่ ฝน การควบแน่น และไอน้ำ น้ำเป็นอิเล็กโทรไลต์ที่ละลายไอออนที่มีฤทธิ์กัดกร่อนจำนวนมากซึ่งกัดกร่อนโลหะ เมื่ออุณหภูมิของส่วนหนึ่งของอุปกรณ์ต่ำกว่า "จุดน้ำค้าง" (อุณหภูมิ) จะเกิดการควบแน่นบนพื้นผิว: ชิ้นส่วนโครงสร้างหรือ PCBA
ฝุ่น
มีฝุ่นละอองในบรรยากาศ มลพิษไอออนดูดซับฝุ่นเกาะอยู่ภายในอุปกรณ์อิเล็กทรอนิกส์และทำให้เกิดความล้มเหลว นี่เป็นปัญหาทั่วไปเกี่ยวกับความล้มเหลวทางอิเล็กทรอนิกส์ในภาคสนาม
ฝุ่นแบ่งออกเป็นสองประเภท: ฝุ่นหยาบมีเส้นผ่านศูนย์กลาง 2.5 ~ 15 ไมครอนของอนุภาคที่ผิดปกติ โดยทั่วไปจะไม่ทำให้เกิดข้อผิดพลาด ส่วนโค้ง และปัญหาอื่น ๆ แต่ส่งผลกระทบต่อหน้าสัมผัสของตัวเชื่อมต่อ ฝุ่นละเอียดเป็นอนุภาคที่ผิดปกติซึ่งมีเส้นผ่านศูนย์กลางน้อยกว่า 2.5 ไมครอน ฝุ่นละเอียดมีการยึดเกาะกับ PCBA (แผ่นไม้อัด) ซึ่งสามารถขจัดออกได้ด้วยแปรงป้องกันไฟฟ้าสถิตเท่านั้น
อันตรายจากฝุ่น: ก. เนื่องจากฝุ่นเกาะอยู่บนพื้นผิวของ PCBA ทำให้เกิดการกัดกร่อนทางเคมีไฟฟ้า และอัตราความล้มเหลวเพิ่มขึ้น ข. ฝุ่น + ความร้อนชื้น + หมอกเกลือสร้างความเสียหายให้กับ PCBA มากที่สุด และความล้มเหลวของอุปกรณ์อิเล็กทรอนิกส์เกิดขึ้นมากที่สุดในอุตสาหกรรมเคมีและพื้นที่เหมืองแร่ใกล้ชายฝั่ง ทะเลทราย (พื้นที่ดินเค็ม-ด่าง) และทางใต้ของแม่น้ำ Huaihe ในช่วงโรคราน้ำค้างและ ฤดูฝน
ดังนั้นการป้องกันฝุ่นจึงเป็นส่วนสำคัญของผลิตภัณฑ์
สเปรย์เกลือ
การก่อตัวของสเปรย์เกลือ:สเปรย์เกลือเกิดจากปัจจัยทางธรรมชาติ เช่น คลื่นทะเล กระแสน้ำ ความกดอากาศในการไหลเวียนของบรรยากาศ (มรสุม) แสงแดด และอื่นๆ มันจะลอยเข้ามาตามลม และสมาธิจะลดลงตามระยะห่างจากชายฝั่ง โดยปกติความเข้มข้นของสเปรย์เกลือจะอยู่ที่ 1% ของชายฝั่งเมื่ออยู่ห่างจากชายฝั่ง 1 กม. (แต่จะพัดได้ไกลกว่าในช่วงไต้ฝุ่น)
อันตรายจากสเปรย์เกลือ:ก. ทำให้การเคลือบชิ้นส่วนโครงสร้างโลหะเสียหาย ข. การเร่งความเร็วของการกัดกร่อนด้วยไฟฟ้าเคมีทำให้เกิดการแตกหักของลวดโลหะและความล้มเหลวของส่วนประกอบ
แหล่งที่มาของการกัดกร่อนที่คล้ายกัน:ก. เหงื่อที่มือประกอบด้วยเกลือ ยูเรีย กรดแลคติค และสารเคมีอื่นๆ ซึ่งมีฤทธิ์กัดกร่อนต่ออุปกรณ์อิเล็กทรอนิกส์เช่นเดียวกับสเปรย์เกลือ ดังนั้นควรสวมถุงมือระหว่างการประกอบหรือการใช้งาน และไม่ควรสัมผัสสารเคลือบด้วยมือเปล่า ข. มีฮาโลเจนและกรดอยู่ในฟลักซ์ ซึ่งควรทำความสะอาดและควบคุมความเข้มข้นที่ตกค้าง
ดังนั้นการป้องกันสเปรย์เกลือจึงเป็นส่วนสำคัญในการปกป้องผลิตภัณฑ์
แม่พิมพ์
โรคราน้ำค้างซึ่งเป็นชื่อสามัญของเชื้อราที่มีเส้นใยหมายถึง "เชื้อราที่ขึ้นรา" มีแนวโน้มที่จะก่อตัวเป็นไมซีเลียมที่อุดมสมบูรณ์ แต่ไม่สร้างผลขนาดใหญ่เช่นเห็ด ในสถานที่ชื้นและอบอุ่น สิ่งของจำนวนมากจะเติบโตได้ด้วยตาเปล่า บางส่วนเป็นอาณานิคมที่มีรูปร่างคลุมเครือ ตกตะกอน หรือเป็นใยแมงมุม ซึ่งก็คือเชื้อรา
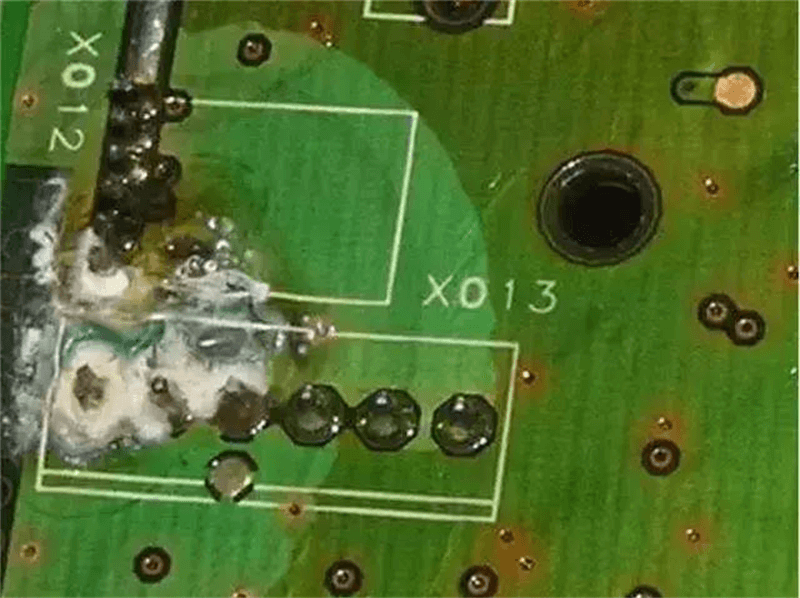
มะเดื่อ. 5: ปรากฏการณ์โรคราน้ำค้าง PCB
อันตรายจากเชื้อรา: ก. การทำลายเซลล์ของเชื้อราและการแพร่กระจายทำให้ฉนวนของสารอินทรีย์ลดลง ความเสียหาย และความล้มเหลว ข. สารเมตาบอไลต์ของเชื้อราคือกรดอินทรีย์ ซึ่งส่งผลต่อความเป็นฉนวนและความแข็งแรงทางไฟฟ้า และทำให้เกิดอาร์คไฟฟ้า
ดังนั้นสารป้องกันเชื้อราจึงเป็นส่วนสำคัญของผลิตภัณฑ์ป้องกัน
เมื่อพิจารณาด้านต่างๆ ข้างต้นแล้ว จะต้องรับประกันความน่าเชื่อถือของผลิตภัณฑ์ได้ดีขึ้น โดยจะต้องแยกออกจากสภาพแวดล้อมภายนอกให้ต่ำที่สุดเท่าที่จะเป็นไปได้ ดังนั้นจึงเริ่มกระบวนการเคลือบรูปทรง
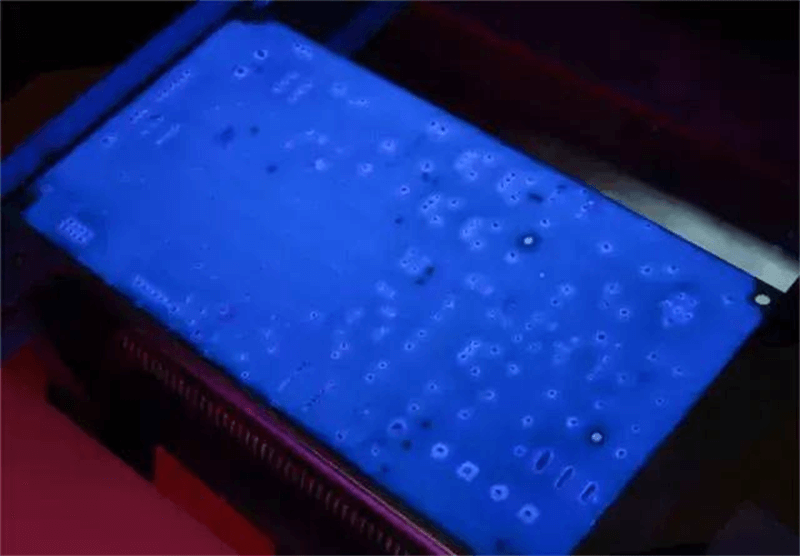
การเคลือบ PCB หลังจากกระบวนการเคลือบ ภายใต้เอฟเฟกต์การถ่ายภาพโคมไฟสีม่วง การเคลือบแบบเดิมสามารถสวยงามมาก!
เคลือบป้องกันสีสามสีหมายถึงการเคลือบชั้นฉนวนป้องกันบาง ๆ บนพื้นผิวของ PCB เป็นวิธีการเคลือบหลังการเชื่อมที่ใช้กันมากที่สุดในปัจจุบัน บางครั้งเรียกว่าการเคลือบพื้นผิวและการเคลือบคอนฟอร์เมนทัล (ชื่อภาษาอังกฤษ: การเคลือบ, การเคลือบคอนฟอร์เมนทัล) จะแยกชิ้นส่วนอิเล็กทรอนิกส์ที่มีความละเอียดอ่อนออกจากสภาพแวดล้อมที่รุนแรง สามารถปรับปรุงความปลอดภัยและความน่าเชื่อถือของผลิตภัณฑ์อิเล็กทรอนิกส์ได้อย่างมาก และยืดอายุการใช้งานของผลิตภัณฑ์ การเคลือบป้องกันสีสามแบบสามารถป้องกันวงจร/ส่วนประกอบจากปัจจัยด้านสิ่งแวดล้อม เช่น ความชื้น มลพิษ การกัดกร่อน ความเครียด การกระแทก การสั่นสะเทือนทางกล และวงจรความร้อน ในขณะเดียวกันก็ปรับปรุงความแข็งแรงเชิงกลและลักษณะฉนวนของผลิตภัณฑ์
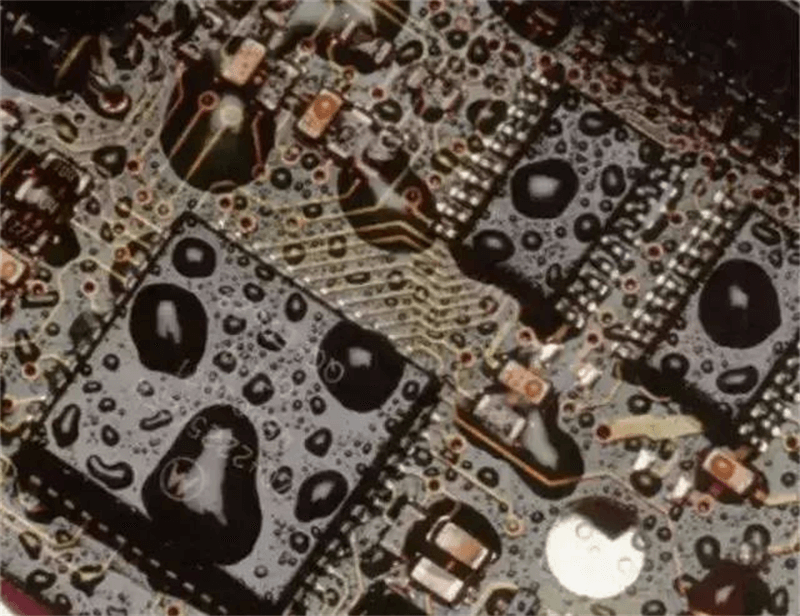
หลังจากกระบวนการเคลือบ PCB สร้างฟิล์มป้องกันโปร่งใสบนพื้นผิว สามารถป้องกันการบุกรุกของน้ำและความชื้นได้อย่างมีประสิทธิภาพ หลีกเลี่ยงการรั่วไหลและการลัดวงจร
2. ประเด็นหลักของกระบวนการเคลือบ
ตามข้อกำหนดของ IPC-A-610E (มาตรฐานการทดสอบการประกอบอิเล็กทรอนิกส์) ส่วนใหญ่จะสะท้อนให้เห็นในด้านต่อไปนี้:
ภูมิภาค
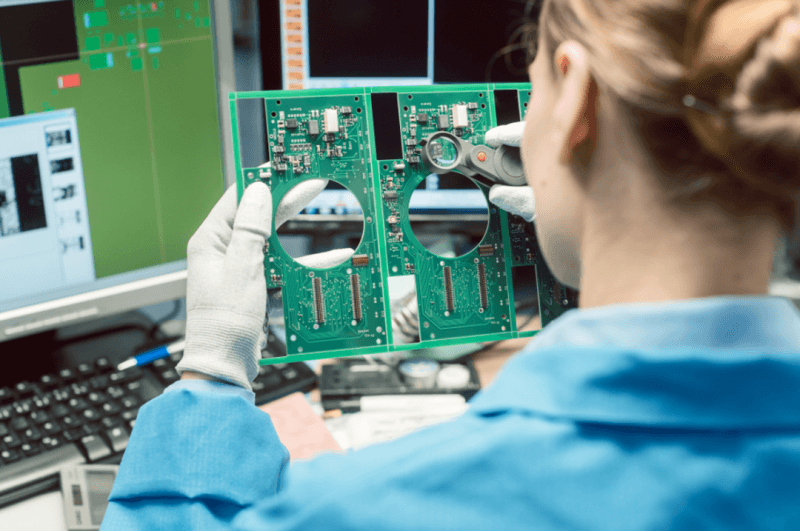
1. บริเวณที่ไม่สามารถเคลือบได้:
พื้นที่ที่ต้องการการเชื่อมต่อทางไฟฟ้า เช่น แผ่นทอง นิ้วทอง รูทะลุโลหะ รูทดสอบ
แบตเตอรี่และอุปกรณ์ยึดแบตเตอรี่
ขั้วต่อ;
ฟิวส์และปลอก;
อุปกรณ์กระจายความร้อน
สายจัมเปอร์;
เลนส์ของอุปกรณ์ออปติคอล
โพเทนชิออมิเตอร์;
เซ็นเซอร์;
ไม่มีสวิตช์ที่ปิดสนิท
พื้นที่อื่นๆ ที่การเคลือบอาจส่งผลต่อประสิทธิภาพหรือการทำงาน
2.บริเวณที่ต้องเคลือบ: ข้อต่อบัดกรี หมุด ส่วนประกอบ และตัวนำทั้งหมด
3. พื้นที่เสริม
ความหนา
วัดความหนาบนพื้นผิวเรียบไม่มีอุปสรรคและบ่มแล้วของส่วนประกอบวงจรพิมพ์หรือบนแผ่นที่แนบมาซึ่งผ่านกระบวนการกับส่วนประกอบนั้น แผงที่แนบมาอาจเป็นวัสดุเดียวกับแผงพิมพ์หรือวัสดุอื่นที่ไม่มีรูพรุน เช่น โลหะหรือแก้ว การวัดความหนาของฟิล์มเปียกยังสามารถใช้เป็นวิธีการเสริมในการวัดความหนาของชั้นเคลือบได้ ตราบใดที่มีความสัมพันธ์ในการแปลงสภาพระหว่างความหนาของฟิล์มเปียกและแห้งที่บันทึกไว้

ตารางที่ 1: มาตรฐานช่วงความหนาของวัสดุเคลือบแต่ละประเภท
วิธีทดสอบความหนา:
1. เครื่องมือวัดความหนาของฟิล์มแห้ง: ไมโครมิเตอร์ (IPC-CC-830B); b เครื่องทดสอบความหนาของฟิล์มแห้ง (ฐานเหล็ก)
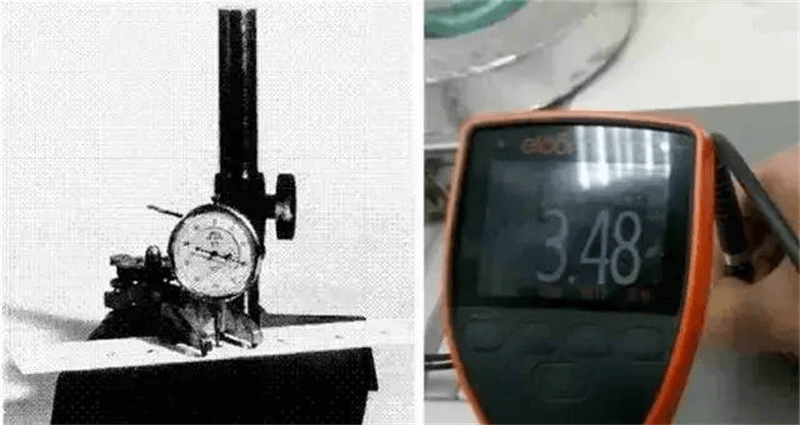
รูปที่ 9 อุปกรณ์ฟิล์มแห้งไมโครมิเตอร์
2. การวัดความหนาของฟิล์มเปียก: ความหนาของฟิล์มเปียกสามารถรับได้โดยเครื่องมือวัดความหนาของฟิล์มเปียกแล้วคำนวณโดยสัดส่วนของปริมาณของแข็งของกาว
ความหนาของฟิล์มแห้ง
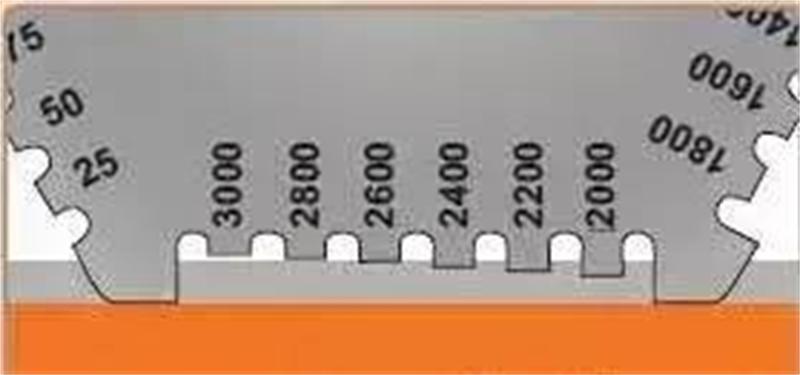
ในรูปที่ 10 ความหนาของฟิล์มเปียกได้มาจากเครื่องทดสอบความหนาของฟิล์มเปียก จากนั้นคำนวณความหนาของฟิล์มแห้ง
ความละเอียดของขอบ
คำนิยาม: ภายใต้สถานการณ์ปกติ วาล์วสเปรย์ที่พ่นออกมาจากขอบเส้นจะไม่ตรงมากนัก และจะมีเสี้ยนอยู่บ้างเสมอ เรากำหนดความกว้างของเสี้ยนเป็นความละเอียดของขอบ ดังที่แสดงด้านล่าง ขนาดของ d คือค่าความละเอียดของขอบ
หมายเหตุ: ความละเอียดของขอบยิ่งน้อยก็ยิ่งดี แต่ความต้องการของลูกค้าที่แตกต่างกันจะไม่เหมือนกัน ดังนั้นความละเอียดของขอบเคลือบเฉพาะตราบเท่าที่ตรงตามความต้องการของลูกค้า

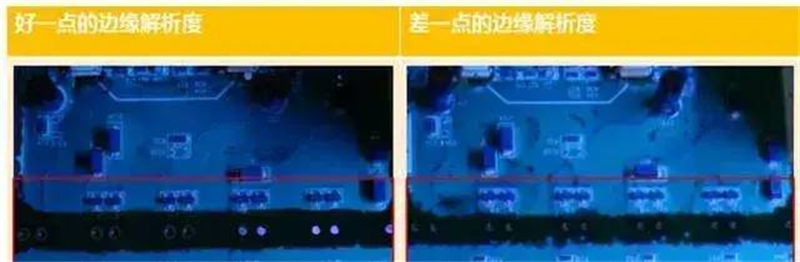
รูปที่ 11: การเปรียบเทียบความละเอียดของขอบ
ความสม่ำเสมอ
กาวควรมีลักษณะเป็นความหนาสม่ำเสมอและฟิล์มเรียบและโปร่งใสที่ปกคลุมอยู่ในผลิตภัณฑ์โดยเน้นที่ความสม่ำเสมอของกาวที่ปกคลุมอยู่ในผลิตภัณฑ์เหนือพื้นที่ จากนั้นจะต้องมีความหนาเท่ากัน ไม่มีปัญหาในกระบวนการ: รอยแตกร้าว การแบ่งชั้น เส้นสีส้ม มลพิษ ปรากฏการณ์ของเส้นเลือดฝอย ฟองอากาศ
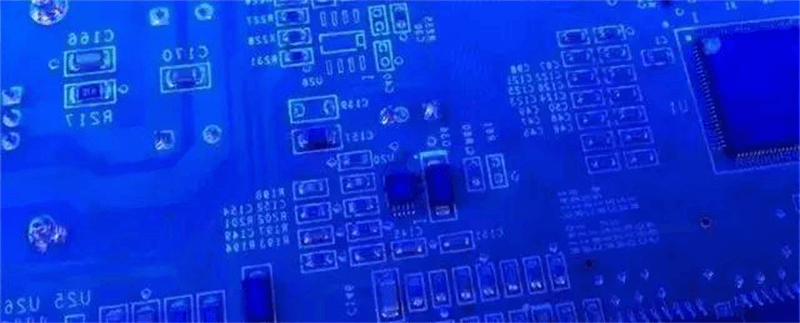
รูปที่ 12: ผลการเคลือบเครื่องเคลือบอัตโนมัติซีรีส์ AC อัตโนมัติตามแนวแกนความสม่ำเสมอสม่ำเสมอมาก
3. การตระหนักถึงกระบวนการเคลือบ
กระบวนการเคลือบ
1 เตรียมตัว
เตรียมผลิตภัณฑ์และกาวและสิ่งของที่จำเป็นอื่น ๆ
กำหนดตำแหน่งของการคุ้มครองในพื้นที่
กำหนดรายละเอียดกระบวนการที่สำคัญ
2: ล้าง
ควรทำความสะอาดให้เร็วที่สุดหลังการเชื่อม เพื่อป้องกันสิ่งสกปรกจากการเชื่อมทำความสะอาดได้ยาก
ตรวจสอบว่ามลพิษหลักมีขั้วหรือไม่มีขั้ว เพื่อเลือกสารทำความสะอาดที่เหมาะสม
หากใช้สารทำความสะอาดแอลกอฮอล์ ต้องคำนึงถึงเรื่องความปลอดภัย: ต้องมีกฎการระบายอากาศที่ดี การทำความเย็น และการอบแห้งหลังการล้าง เพื่อป้องกันการระเหยของตัวทำละลายที่ตกค้างซึ่งเกิดจากการระเบิดในเตาอบ
การทำความสะอาดน้ำด้วยน้ำยาทำความสะอาดอัลคาไลน์ (อิมัลชัน) เพื่อล้างฟลักซ์แล้วล้างออกด้วยน้ำบริสุทธิ์เพื่อทำความสะอาดของเหลวทำความสะอาดเพื่อให้เป็นไปตามมาตรฐานการทำความสะอาด
3. การป้องกันการมาสก์ (หากไม่มีการใช้อุปกรณ์เคลือบแบบเลือกสรร) นั่นคือ หน้ากาก
ควรเลือกฟิล์มชนิดไม่ยึดติดจะไม่ทำให้เทปกระดาษหลุดร่อน
ควรใช้เทปกระดาษป้องกันไฟฟ้าสถิตในการป้องกัน IC
ตามความต้องการของภาพวาดสำหรับอุปกรณ์บางชนิดเพื่อป้องกันการป้องกัน
4. ลดความชื้น
หลังจากทำความสะอาด PCBA ที่มีฉนวนหุ้ม (ส่วนประกอบ) จะต้องทำให้แห้งและลดความชื้นก่อนการเคลือบ
กำหนดอุณหภูมิ/เวลาในการทำให้แห้งล่วงหน้าตามอุณหภูมิที่อนุญาตโดย PCBA (ส่วนประกอบ)
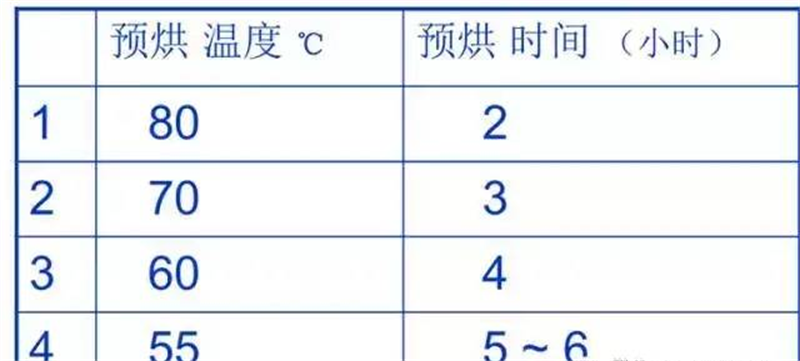
PCBA (ส่วนประกอบ) สามารถกำหนดอุณหภูมิ/เวลาของโต๊ะอบแห้งได้
5 เคลือบ
กระบวนการเคลือบรูปร่างขึ้นอยู่กับข้อกำหนดในการป้องกัน PCBA อุปกรณ์กระบวนการที่มีอยู่ และการสำรองทางเทคนิคที่มีอยู่ ซึ่งโดยปกติแล้วจะทำได้ด้วยวิธีต่อไปนี้:
ก. แปรงด้วยมือ
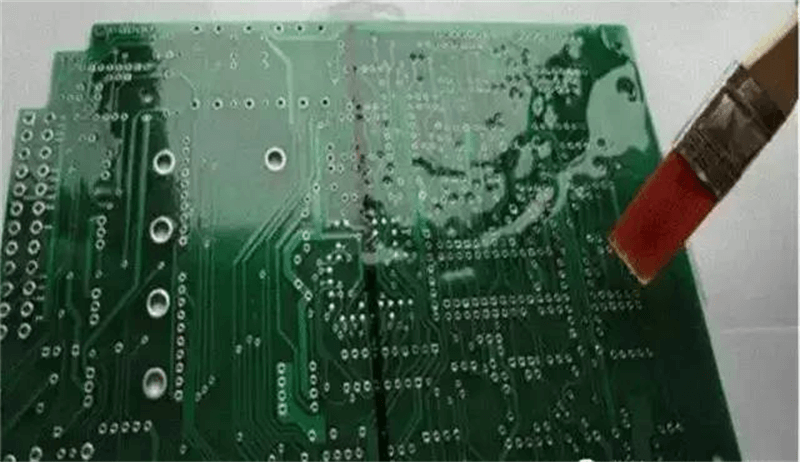
รูปที่ 13: วิธีการแปรงด้วยมือ
การเคลือบแปรงเป็นกระบวนการที่ใช้กันอย่างแพร่หลาย เหมาะสำหรับการผลิตชุดเล็ก โครงสร้าง PCBA ซับซ้อนและหนาแน่น จำเป็นต้องปกป้องข้อกำหนดการป้องกันของผลิตภัณฑ์ที่รุนแรง เนื่องจากสามารถควบคุมการเคลือบแปรงได้อย่างอิสระ ดังนั้นส่วนที่ไม่ได้รับอนุญาตให้ทาสีจะไม่ปนเปื้อน
การเคลือบแปรงใช้วัสดุน้อยที่สุดเหมาะสำหรับราคาที่สูงขึ้นของสีสององค์ประกอบ
กระบวนการพ่นสีมีข้อกำหนดสูงสำหรับผู้ปฏิบัติงาน ก่อนการก่อสร้าง ควรแยกแยะข้อกำหนดเกี่ยวกับภาพวาดและการเคลือบอย่างระมัดระวัง ชื่อของส่วนประกอบ PCBA ควรได้รับการยอมรับ และส่วนที่ไม่ได้รับอนุญาตให้เคลือบควรมีเครื่องหมายที่สะดุดตา
ไม่อนุญาตให้ผู้ปฏิบัติงานสัมผัสปลั๊กอินที่พิมพ์ด้วยมือเมื่อใดก็ได้เพื่อหลีกเลี่ยงการปนเปื้อน
ข.จุ่มด้วยมือ
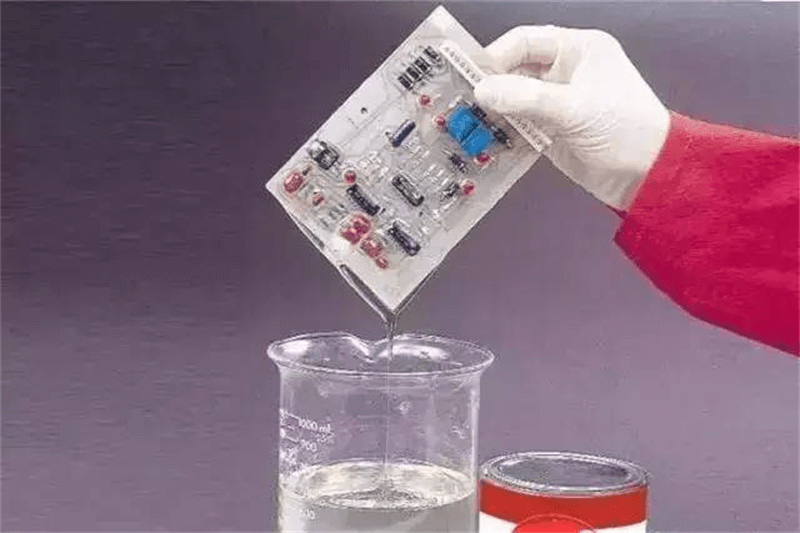
รูปที่ 14: วิธีการเคลือบแบบจุ่มมือ
กระบวนการเคลือบแบบจุ่มให้ผลลัพธ์การเคลือบที่ดีที่สุด PCBA สามารถเคลือบสม่ำเสมอและต่อเนื่องกับส่วนต่างๆ ของ PCBA ได้ กระบวนการเคลือบแบบจุ่มไม่เหมาะสำหรับ PCbas ที่มีตัวเก็บประจุแบบปรับได้ แกนแม่เหล็กแบบละเอียด โพเทนชิโอมิเตอร์ แกนแม่เหล็กรูปถ้วย และชิ้นส่วนบางส่วนมีการปิดผนึกไม่ดี
พารามิเตอร์ที่สำคัญของกระบวนการเคลือบแบบจุ่ม:
ปรับความหนืดที่เหมาะสม
ควบคุมความเร็วในการยก PCBA เพื่อป้องกันไม่ให้เกิดฟองอากาศ โดยปกติจะไม่เกิน 1 เมตรต่อวินาที
ค. การฉีดพ่น
การพ่นเป็นวิธีที่ใช้กันอย่างแพร่หลายและง่ายต่อการยอมรับ โดยแบ่งเป็น 2 ประเภท ดังนี้
1 การฉีดพ่นด้วยมือ
รูปที่ 15: วิธีการฉีดพ่นแบบแมนนวล
เหมาะสำหรับชิ้นงานที่มีความซับซ้อนมากขึ้น ยากที่จะพึ่งพาสถานการณ์การผลิตจำนวนมากของอุปกรณ์อัตโนมัติ นอกจากนี้ยังเหมาะสำหรับความหลากหลายของสายผลิตภัณฑ์ แต่สถานการณ์น้อย สามารถพ่นไปยังตำแหน่งพิเศษมากขึ้น
หมายเหตุสำหรับการฉีดพ่นด้วยตนเอง: ละอองสีจะทำให้อุปกรณ์บางชนิดเสียหาย เช่น ปลั๊ก PCB, ช่องเสียบ IC, หน้าสัมผัสที่ละเอียดอ่อนบางส่วน และชิ้นส่วนที่ต่อสายดินบางส่วน ชิ้นส่วนเหล่านี้จำเป็นต้องคำนึงถึงความน่าเชื่อถือของการป้องกันที่กำบัง อีกประเด็นหนึ่งคือผู้ปฏิบัติงานไม่ควรสัมผัสปลั๊กที่พิมพ์ด้วยมือตลอดเวลาเพื่อป้องกันการปนเปื้อนของพื้นผิวสัมผัสปลั๊ก
2. การฉีดพ่นอัตโนมัติ
โดยทั่วไปหมายถึงการพ่นอัตโนมัติด้วยอุปกรณ์การเคลือบแบบเลือกสรร เหมาะสำหรับการผลิตจำนวนมาก ความสม่ำเสมอที่ดี ความแม่นยำสูง มลภาวะต่อสิ่งแวดล้อมน้อย ด้วยการยกระดับของอุตสาหกรรม การเพิ่มขึ้นของต้นทุนแรงงาน และข้อกำหนดที่เข้มงวดในการปกป้องสิ่งแวดล้อม อุปกรณ์ฉีดพ่นอัตโนมัติจะค่อยๆ เข้ามาแทนที่วิธีการเคลือบอื่นๆ
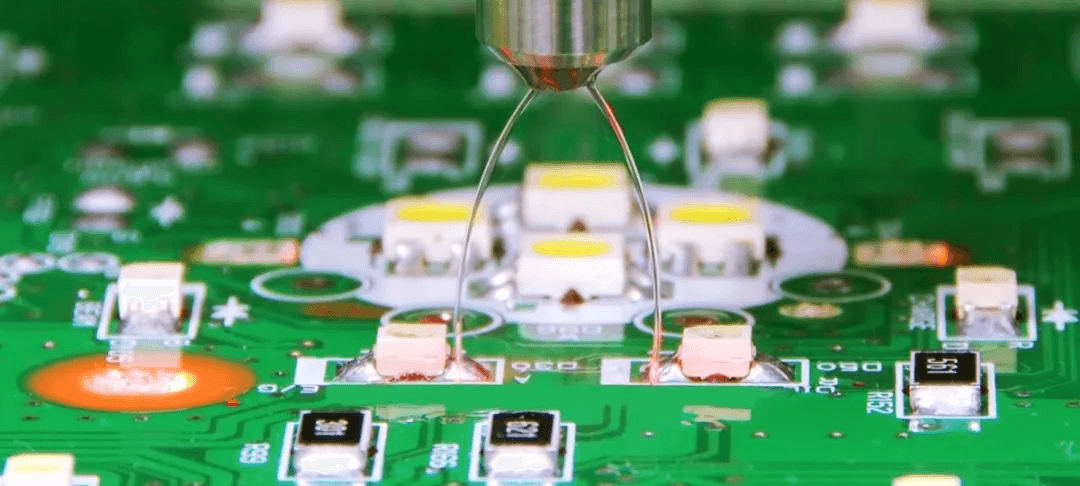
ด้วยความต้องการระบบอัตโนมัติที่เพิ่มขึ้นของอุตสาหกรรม 4.0 จุดเน้นของอุตสาหกรรมได้เปลี่ยนจากการจัดหาอุปกรณ์การเคลือบที่เหมาะสมไปเป็นการแก้ปัญหาของกระบวนการเคลือบทั้งหมด เครื่องเคลือบแบบเลือกสีอัตโนมัติ - เคลือบได้แม่นยำและไม่เปลืองวัสดุ เหมาะสำหรับการเคลือบปริมาณมาก เหมาะที่สุดสำหรับการเคลือบสารกันสี 3 ชนิดในปริมาณมาก
การเปรียบเทียบของเครื่องเคลือบอัตโนมัติและกระบวนการเคลือบแบบดั้งเดิม
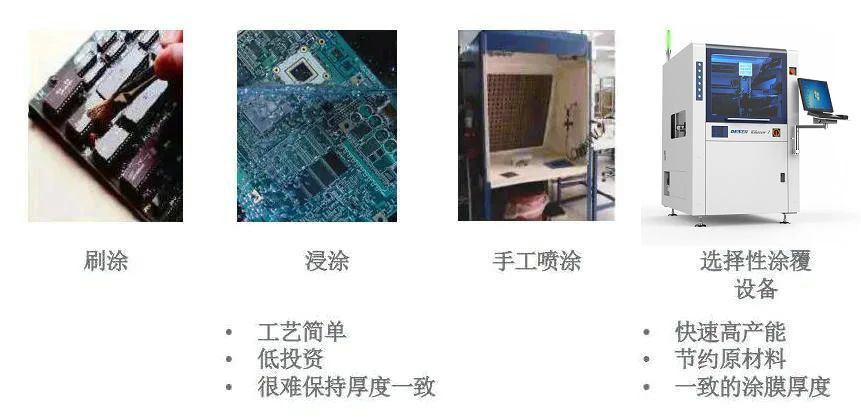
การเคลือบสีสามหลักฐาน PCBA แบบดั้งเดิม:
1) การเคลือบแปรง: มีฟองคลื่นแปรงกำจัดขน
2) การเขียน: ช้าเกินไป ไม่สามารถควบคุมความแม่นยำได้
3) แช่ทั้งชิ้น: สีสิ้นเปลืองเกินไป, ความเร็วช้า;
4) การฉีดพ่นด้วยปืนสเปรย์: เพื่อติดตั้งการป้องกันการดริฟท์มากเกินไป
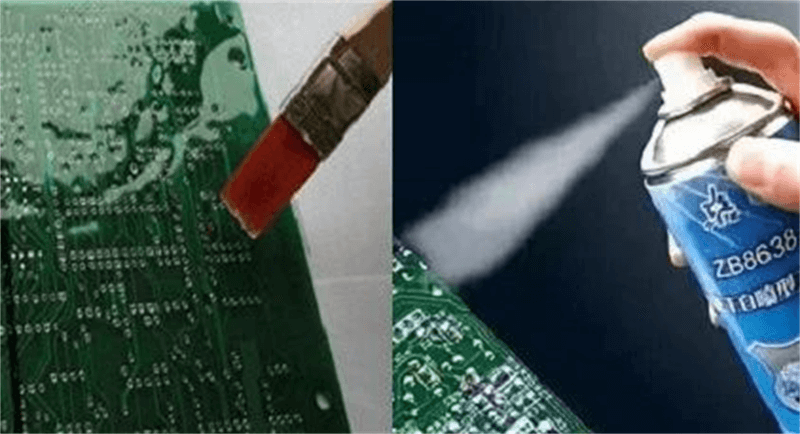
การเคลือบเครื่องเคลือบ:
1) จำนวนการพ่นสี ตำแหน่งการพ่นสี และพื้นที่ได้รับการตั้งค่าอย่างถูกต้อง และไม่จำเป็นต้องเพิ่มคนมาเช็ดกระดานหลังจากการพ่นสี
2) ส่วนประกอบปลั๊กอินบางตัวที่มีระยะห่างจากขอบจานมากสามารถทาสีได้โดยตรงโดยไม่ต้องติดตั้งฟิกซ์เจอร์ ช่วยประหยัดบุคลากรในการติดตั้งเพลต
3) ไม่มีการระเหยของก๊าซเพื่อให้แน่ใจว่าสภาพแวดล้อมการทำงานที่สะอาด
4) วัสดุพิมพ์ทั้งหมดไม่จำเป็นต้องใช้ฟิกซ์เจอร์เพื่อปกปิดฟิล์มคาร์บอน ช่วยลดโอกาสที่จะเกิดการชนกัน
5) ความหนาเคลือบป้องกันสีสามชุดช่วยปรับปรุงประสิทธิภาพการผลิตและคุณภาพของผลิตภัณฑ์อย่างมาก แต่ยังหลีกเลี่ยงการสูญเสียสี
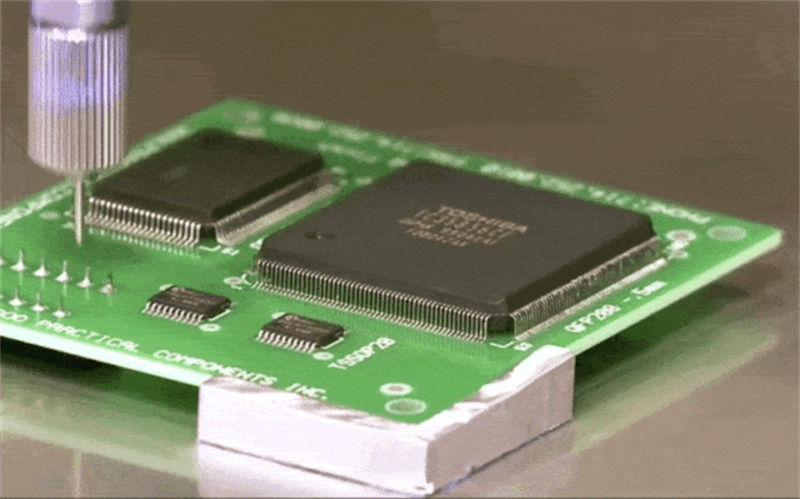
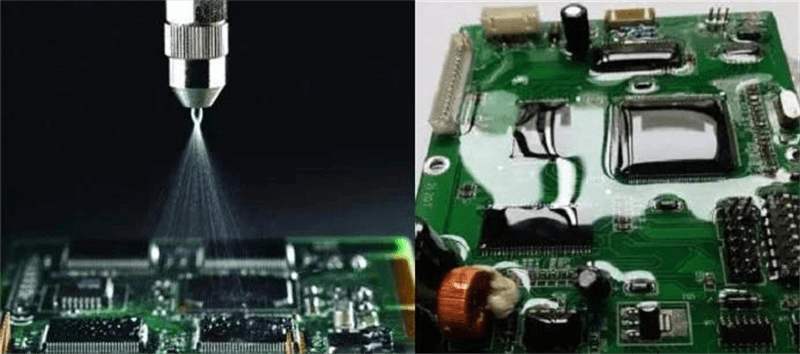
เครื่องเคลือบสีป้องกันสีอัตโนมัติ PCBA สามเครื่องได้รับการออกแบบมาเป็นพิเศษสำหรับพ่นอุปกรณ์พ่นอัจฉริยะป้องกันสีสามสี เนื่องจากวัสดุที่จะพ่นและของเหลวที่ใช้ฉีดพ่นแตกต่างกัน เครื่องเคลือบในการก่อสร้างการเลือกส่วนประกอบอุปกรณ์ก็แตกต่างกัน เครื่องเคลือบป้องกันสีสามเครื่องใช้โปรแกรมควบคุมคอมพิวเตอร์ล่าสุด สามารถรับรู้การเชื่อมโยงแบบสามแกน ขณะเดียวกันก็ติดตั้งระบบกำหนดตำแหน่งและติดตามกล้อง สามารถควบคุมพื้นที่ฉีดพ่นได้อย่างแม่นยำ
เครื่องเคลือบสีป้องกันสีสามเครื่องหรือที่เรียกว่าเครื่องกาวป้องกันสีสามเครื่อง, เครื่องกาวสเปรย์ป้องกันสีสามเครื่อง, เครื่องสเปรย์น้ำมันป้องกันสีสามเครื่อง, เครื่องสเปรย์ป้องกันสีสามเครื่อง, มีไว้สำหรับการควบคุมของเหลวโดยเฉพาะบนพื้นผิว PCB เคลือบด้วยชั้นป้องกันสี 3 ชั้น เช่น วิธีการเคลือบ การพ่น หรือการหมุนบนพื้นผิว PCB ที่เคลือบด้วยชั้นสารต้านทานแสง
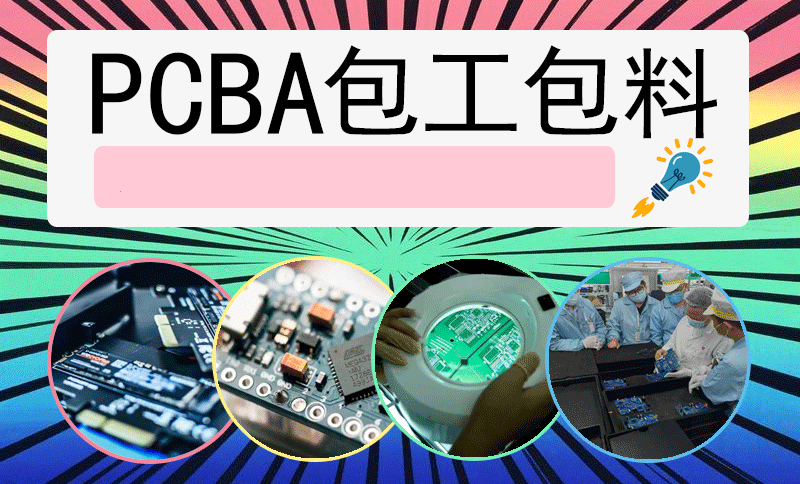
วิธีแก้ปัญหาความต้องการเคลือบสีป้องกันยุคใหม่สามประการได้กลายเป็นปัญหาเร่งด่วนที่ต้องแก้ไขในอุตสาหกรรม อุปกรณ์เคลือบอัตโนมัติที่แสดงโดยเครื่องเคลือบแบบเลือกความแม่นยำนำเสนอวิธีการทำงานใหม่เคลือบได้แม่นยำและไม่เปลืองวัสดุเหมาะที่สุดสำหรับการเคลือบป้องกันสีสามสีจำนวนมาก