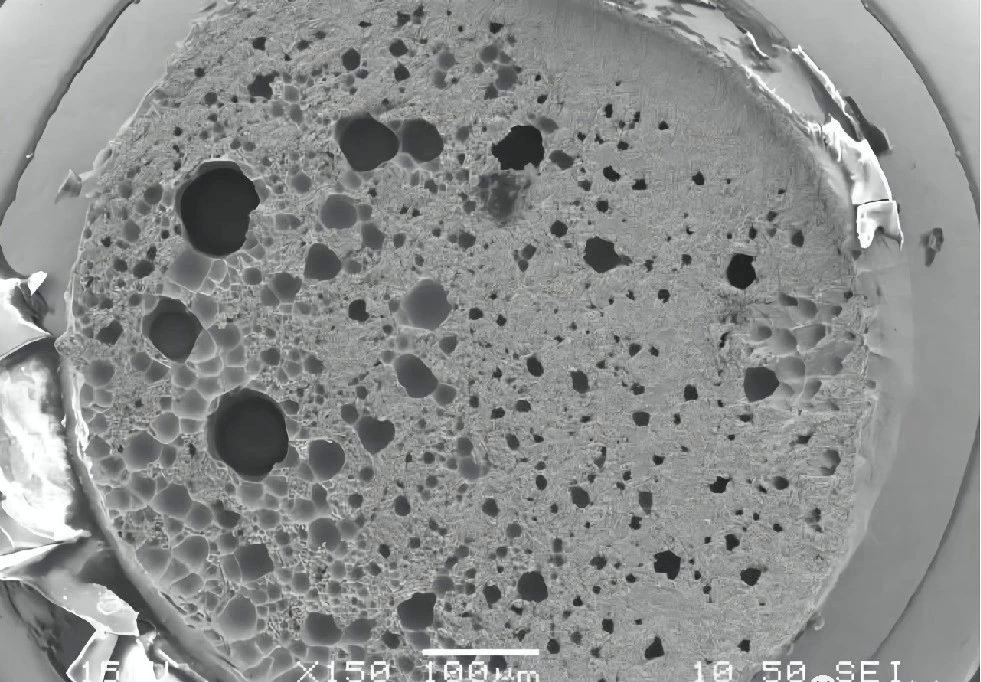
1 บทนำ
ในการประกอบแผงวงจร วางประสานจะถูกพิมพ์บนแผ่นประสานของแผงวงจรก่อน จากนั้นจึงติดส่วนประกอบอิเล็กทรอนิกส์ต่างๆ ในที่สุด หลังจากเตาหลอมละลาย เม็ดบีดดีบุกในสารบัดกรีจะละลาย และชิ้นส่วนอิเล็กทรอนิกส์ทุกชนิดและแผ่นบัดกรีของแผงวงจรจะถูกเชื่อมเข้าด้วยกันเพื่อให้เกิดการประกอบโมดูลย่อยทางไฟฟ้า เทคโนโลยีการติดพื้นผิว (sMT) ถูกนำมาใช้มากขึ้นในผลิตภัณฑ์บรรจุภัณฑ์ที่มีความหนาแน่นสูง เช่น แพ็คเกจระดับระบบ (siP), อุปกรณ์ ballgridarray (BGA) และชิปเปลือยพลังงาน, แพ็คเกจไร้พินแบนสี่เหลี่ยม (quad aatNo-lead เรียกว่า QFN ) อุปกรณ์.
เนื่องจากลักษณะของกระบวนการและวัสดุการเชื่อมแบบบัดกรี หลังจากการเชื่อมแบบรีโฟลว์ของอุปกรณ์พื้นผิวบัดกรีขนาดใหญ่เหล่านี้ จะมีรูในบริเวณการเชื่อมแบบบัดกรี ซึ่งจะส่งผลต่อคุณสมบัติทางไฟฟ้า คุณสมบัติทางความร้อน และคุณสมบัติทางกลของผลิตภัณฑ์ ประสิทธิภาพ และ แม้จะนำไปสู่ความล้มเหลวของผลิตภัณฑ์ ดังนั้นเพื่อปรับปรุงช่องการเชื่อมแบบรีโฟลว์แบบวางบัดกรีจึงกลายเป็นกระบวนการและปัญหาทางเทคนิคที่ต้องแก้ไข นักวิจัยบางคนได้วิเคราะห์และศึกษาสาเหตุของช่องเชื่อมบอลบัดกรี BGA และจัดหาแนวทางการปรับปรุง บัดกรีแบบธรรมดา วางการเชื่อมกระบวนการเชื่อม reflow ขาดพื้นที่ QFN มากกว่า 10 มม.2 หรือพื้นที่การเชื่อมมากกว่า 6 มม.2 ของโซลูชันชิปเปลือย
ใช้การเชื่อมแบบ Preformsolder และการเชื่อมด้วยเตาหลอมสุญญากาศเพื่อปรับปรุงรูเชื่อม การบัดกรีสำเร็จรูปต้องใช้อุปกรณ์พิเศษในการชี้ฟลักซ์ ตัวอย่างเช่น ชิปจะถูกชดเชยและเอียงอย่างจริงจังหลังจากที่ชิปถูกวางลงบนโลหะบัดกรีสำเร็จรูปโดยตรง ถ้าชิปฟลักซ์เมาท์เป็นแบบรีโฟลว์แล้วชี้ กระบวนการจะเพิ่มขึ้น 2 รีโฟลว์ และต้นทุนของการบัดกรีและวัสดุฟลักซ์สำเร็จรูปจะสูงกว่าแบบพอสต์แบบบัดกรีมาก
อุปกรณ์ไหลย้อนสุญญากาศมีราคาแพงกว่า ความจุสุญญากาศของห้องสุญญากาศอิสระต่ำมาก ประสิทธิภาพต้นทุนไม่สูงและปัญหาการกระเด็นของดีบุกเป็นเรื่องร้ายแรง ซึ่งเป็นปัจจัยสำคัญในการประยุกต์ใช้ความหนาแน่นสูงและสนามขนาดเล็ก สินค้า. ในบทความนี้ ตามกระบวนการเชื่อมแบบรีโฟลว์แบบวางประสานแบบดั้งเดิม กระบวนการเชื่อมแบบรีโฟลว์ขั้นที่สองใหม่ได้รับการพัฒนาและแนะนำเพื่อปรับปรุงช่องการเชื่อมและแก้ปัญหาการยึดเกาะและการแตกร้าวของซีลพลาสติกที่เกิดจากช่องเชื่อม
2 ช่องการเชื่อมแบบ reflow การพิมพ์แบบวางประสานและกลไกการผลิต
2.1 ช่องเชื่อม
หลังจากการเชื่อมแบบรีโฟลว์ ผลิตภัณฑ์ได้รับการทดสอบภายใต้การเอ็กซเรย์ พบว่ารูในบริเวณการเชื่อมที่มีสีอ่อนกว่าเกิดจากการบัดกรีในชั้นการเชื่อมไม่เพียงพอ ดังแสดงในรูปที่ 1
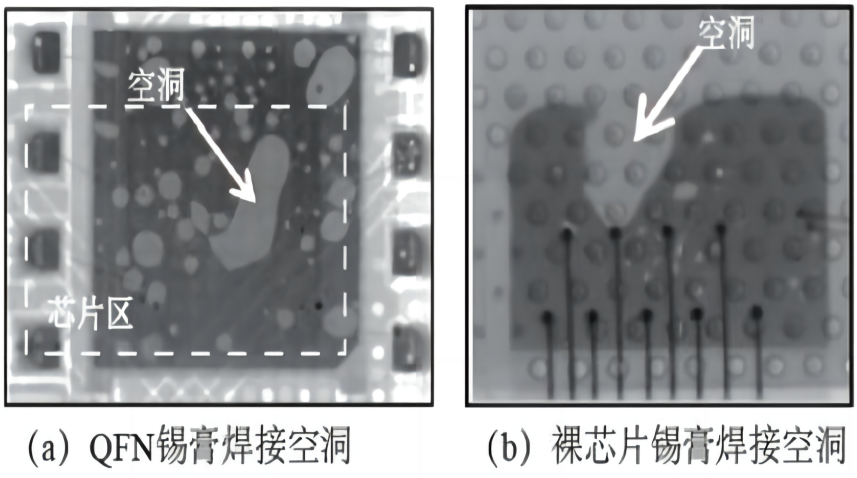
การตรวจจับรังสีเอกซ์ของรูฟอง
2.2 กลไกการเกิดช่องเชื่อม
ยกตัวอย่างการวางบัดกรี sAC305 องค์ประกอบหลักและฟังก์ชันจะแสดงในตารางที่ 1 ฟลักซ์และเม็ดบีดดีบุกถูกเชื่อมเข้าด้วยกันในรูปแบบเพสต์ อัตราส่วนน้ำหนักของการบัดกรีดีบุกต่อฟลักซ์อยู่ที่ประมาณ 9:1 และอัตราส่วนปริมาตรอยู่ที่ประมาณ 1:1
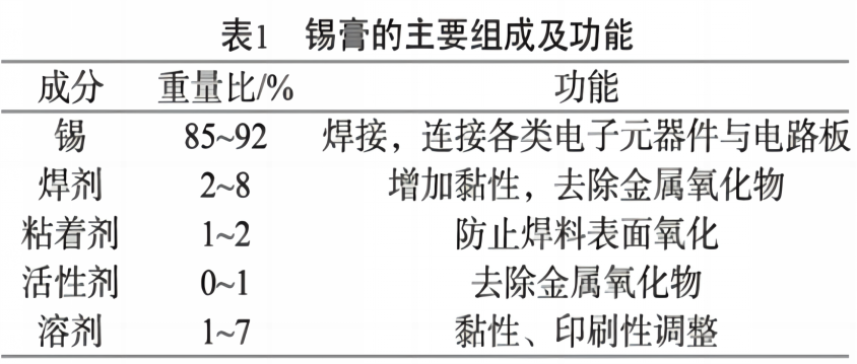
หลังจากพิมพ์และติดตั้งสารบัดกรีด้วยชิ้นส่วนอิเล็กทรอนิกส์ต่างๆ สารบัดกรีจะต้องผ่านการอุ่น การเปิดใช้งาน การไหลย้อนกลับ และการทำให้เย็นลงสี่ขั้นตอนเมื่อผ่านเตาหลอมกรดไหลย้อน สถานะของสารบัดกรีก็แตกต่างกันไปตามอุณหภูมิที่แตกต่างกันในแต่ละขั้นตอน ดังแสดงในรูปที่ 2
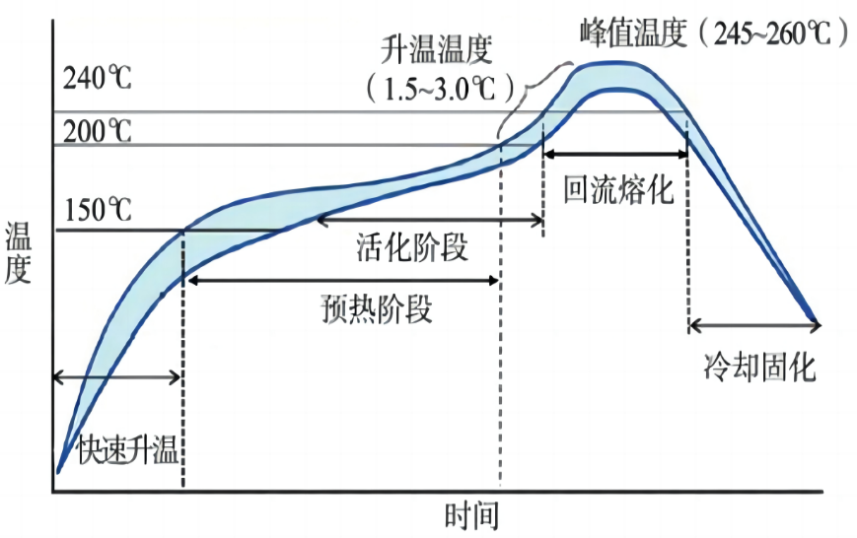
การอ้างอิงโปรไฟล์สำหรับแต่ละพื้นที่ของการบัดกรีแบบรีโฟลว์
ในขั้นตอนการอุ่นเครื่องและกระตุ้นการทำงาน ส่วนประกอบที่ระเหยได้ในฟลักซ์ในสารบัดกรีจะถูกระเหยเป็นแก๊สเมื่อถูกความร้อน ในเวลาเดียวกัน ก๊าซจะถูกสร้างขึ้นเมื่อกำจัดออกไซด์บนพื้นผิวของชั้นการเชื่อมออก ก๊าซเหล่านี้บางส่วนจะระเหยและทิ้งสารบัดกรีไว้ และเม็ดบีดบัดกรีจะถูกควบแน่นแน่นเนื่องจากการระเหยของฟลักซ์ ในระยะไหลย้อน ฟลักซ์ที่เหลือในสารประสานจะระเหยอย่างรวดเร็ว เม็ดบีดดีบุกจะละลาย ก๊าซระเหยฟลักซ์จำนวนเล็กน้อย และอากาศส่วนใหญ่ระหว่างเม็ดบีดดีบุกจะไม่กระจายตามเวลา และสารตกค้างใน ดีบุกหลอมเหลวและอยู่ภายใต้ความตึงเครียดของดีบุกหลอมเหลวเป็นโครงสร้างแซนวิชแฮมเบอร์เกอร์และถูกจับโดยแผ่นประสานของแผงวงจรและชิ้นส่วนอิเล็กทรอนิกส์และก๊าซที่ห่อหุ้มอยู่ในดีบุกเหลวนั้นยากต่อการหลบหนีโดยเพียง การลอยตัวสูงขึ้น เวลาหลอมเหลวส่วนบนสั้นมาก เมื่อดีบุกหลอมเหลวเย็นลงและกลายเป็นดีบุกแข็ง รูขุมขนจะปรากฏขึ้นในชั้นการเชื่อมและเกิดรูบัดกรี ดังแสดงในรูปที่ 3
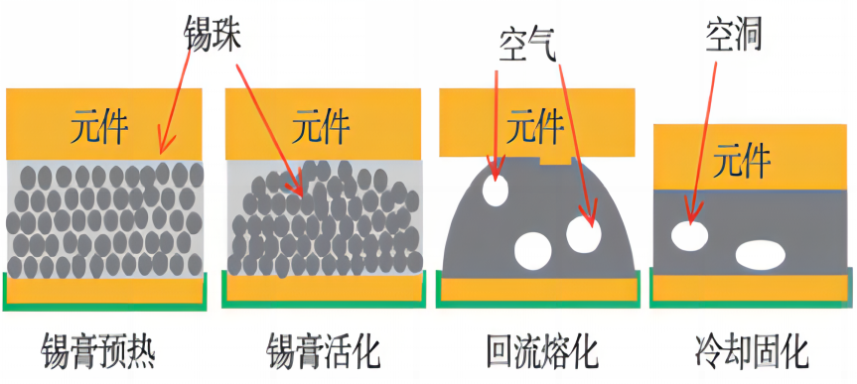
แผนผังของช่องว่างที่เกิดจากการเชื่อมแบบบัดกรีแบบรีโฟลว์
สาเหตุหลักของช่องเชื่อมคืออากาศหรือก๊าซระเหยที่ห่ออยู่ในสารบัดกรีหลังจากการหลอมละลายไม่ได้ระบายออกจนหมด ปัจจัยที่มีอิทธิพล ได้แก่ วัสดุที่บัดกรี, รูปร่างการพิมพ์ของบัดกรี, จำนวนการพิมพ์ของบัดกรี, อุณหภูมิกรดไหลย้อน, เวลากรดไหลย้อน, ขนาดการเชื่อม, โครงสร้างและอื่น ๆ
3. การตรวจสอบปัจจัยที่มีอิทธิพลต่อการพิมพ์รูเชื่อมแบบรีโฟลว์แบบวางประสาน
การทดสอบ QFN และชิปเปลือยใช้เพื่อยืนยันสาเหตุหลักของช่องว่างการเชื่อมแบบรีโฟลว์ และเพื่อค้นหาวิธีปรับปรุงช่องว่างการเชื่อมแบบรีโฟลว์ที่พิมพ์ด้วยสารบัดกรี QFN และโปรไฟล์ผลิตภัณฑ์การเชื่อมแบบ reflow ของชิปเปลือยบัดกรีแสดงในรูปที่ 4 ขนาดพื้นผิวการเชื่อม QFN คือ 4.4 มม. x 4.1 มม. พื้นผิวการเชื่อมเป็นชั้นกระป๋อง (ดีบุกบริสุทธิ์ 100%); ขนาดการเชื่อมของชิปเปลือยคือ 3.0 มม. x 2.3 มม. ชั้นการเชื่อมคือชั้นบิเมทัลลิกนิกเกิลวานาเดียมสปัตเตอร์และชั้นพื้นผิวคือวาเนเดียม แผ่นเชื่อมของซับสเตรตเป็นแบบจุ่มทองนิกเกิล-แพลเลเดียมแบบไม่ใช้ไฟฟ้า และมีความหนา 0.4μm/0.06μm/0.04μm ใช้สารบัดกรี SAC305 อุปกรณ์การพิมพ์สารบัดกรีคือ DEK Horizon APix อุปกรณ์เตาหลอมกรดไหลย้อนคือ BTUPyramax150N และอุปกรณ์เอ็กซเรย์คือ DAGExD7500VR
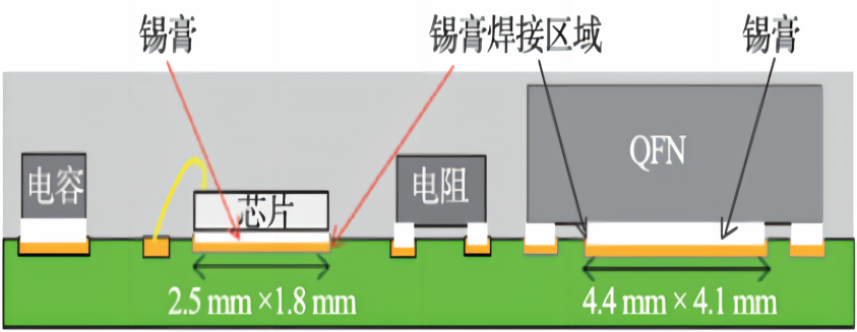
QFN และภาพวาดการเชื่อมชิปเปลือย
เพื่อความสะดวกในการเปรียบเทียบผลการทดสอบ การเชื่อมแบบรีโฟลว์ได้ดำเนินการภายใต้เงื่อนไขในตารางที่ 2
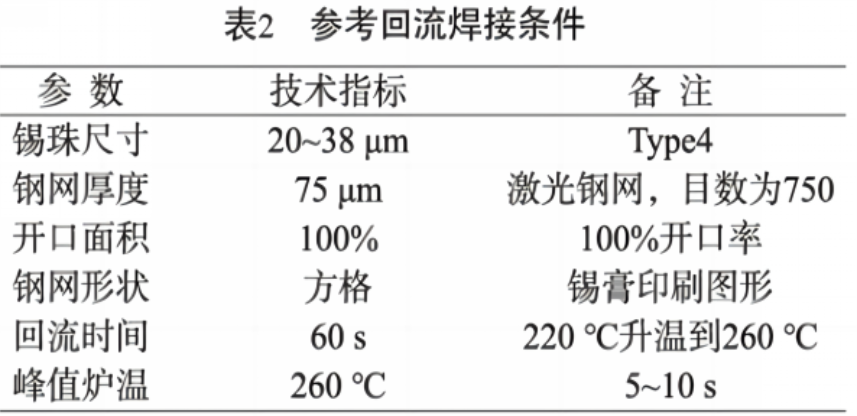
ตารางสภาพการเชื่อมแบบ Reflow
หลังจากการติดตั้งพื้นผิวและการเชื่อมแบบรีโฟลว์เสร็จสมบูรณ์ ชั้นการเชื่อมจะถูกตรวจพบด้วยรังสีเอกซ์ และพบว่ามีรูขนาดใหญ่ในชั้นการเชื่อมที่ด้านล่างของ QFN และชิปเปลือย ดังแสดงในรูปที่ 5
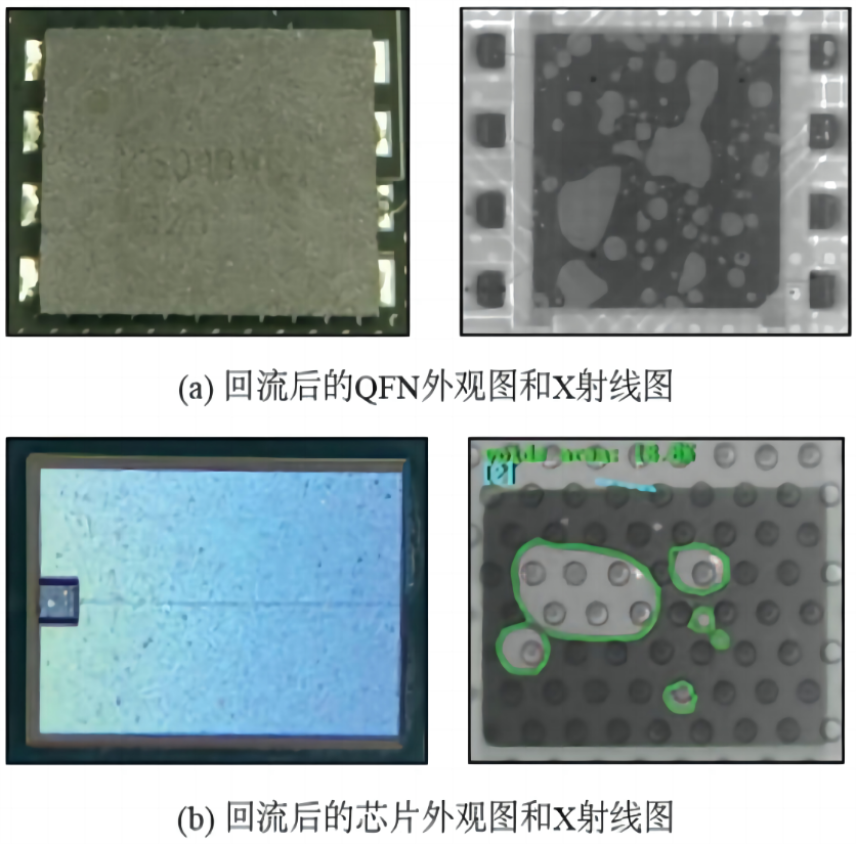
QFN และชิปโฮโลแกรม (เอ็กซ์เรย์)
เนื่องจากขนาดเม็ดบีดดีบุก ความหนาของตาข่ายเหล็ก อัตราพื้นที่เปิด รูปร่างตาข่ายเหล็ก เวลาไหลย้อน และอุณหภูมิเตาสูงสุด ล้วนส่งผลต่อช่องว่างในการเชื่อมแบบรีโฟลว์ จึงมีปัจจัยที่มีอิทธิพลมากมาย ซึ่งจะได้รับการตรวจสอบโดยตรงจากการทดสอบของ DOE และจำนวนการทดลอง กลุ่มจะใหญ่เกินไป จำเป็นต้องคัดกรองอย่างรวดเร็วและกำหนดปัจจัยที่มีอิทธิพลหลักผ่านการทดสอบเปรียบเทียบสหสัมพันธ์ จากนั้นจึงปรับปัจจัยที่มีอิทธิพลหลักให้เหมาะสมยิ่งขึ้นผ่าน DOE
3.1 ขนาดของรูบัดกรีและลูกปัดดีบุกบัดกรี
ด้วยประเภท 3 (ขนาดเม็ดบีด 25-45 μm) การทดสอบการบัดกรีแบบ SAC305 เงื่อนไขอื่นๆ ยังคงไม่เปลี่ยนแปลง หลังจากการรีโฟลว์ จะมีการวัดรูในชั้นบัดกรีและเปรียบเทียบกับครีมบัดกรีประเภท 4 พบว่ารูในชั้นโลหะบัดกรีไม่มีความแตกต่างอย่างมีนัยสำคัญระหว่างสารบัดกรีทั้งสองชนิด บ่งชี้ว่าสารบัดกรีที่มีขนาดเม็ดแตกต่างกันไม่มีอิทธิพลที่ชัดเจนต่อรูในชั้นบัดกรีซึ่งไม่ใช่ปัจจัยที่มีอิทธิพล ดังแสดงไว้ในรูปที่ 6 ตามที่แสดง
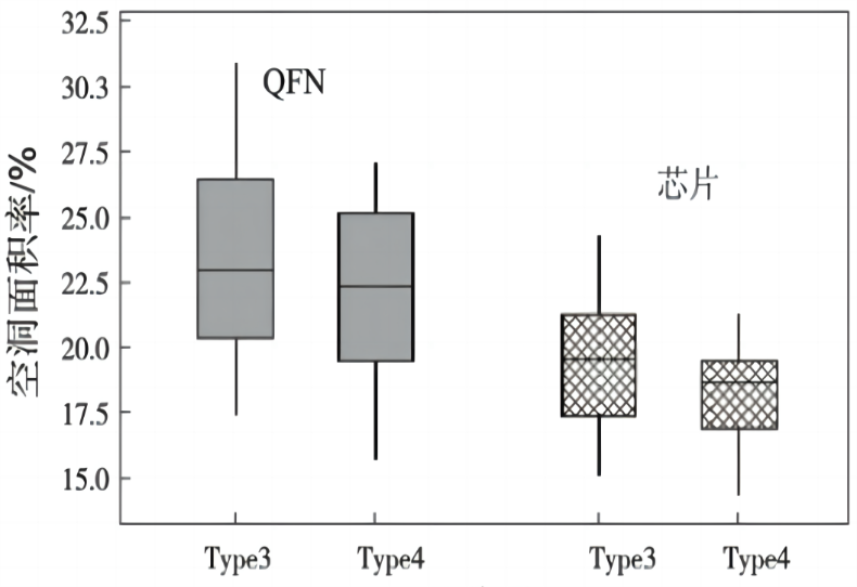
การเปรียบเทียบรูผงดีบุกโลหะที่มีขนาดอนุภาคต่างกัน
3.2 ความหนาของช่องเชื่อมและตาข่ายเหล็กพิมพ์ลาย
หลังจากการรีโฟลว์ พื้นที่โพรงของชั้นเชื่อมจะถูกวัดด้วยตาข่ายเหล็กพิมพ์ที่มีความหนา 50 μm, 100 μm และ 125 μm และเงื่อนไขอื่นๆ ยังคงไม่เปลี่ยนแปลง พบว่าเมื่อเปรียบเทียบผลของความหนาที่แตกต่างกันของตาข่ายเหล็ก (สารบัดกรี) ต่อ QFN กับของตาข่ายเหล็กที่พิมพ์ซึ่งมีความหนา 75 μm เมื่อความหนาของตาข่ายเหล็กเพิ่มขึ้น พื้นที่โพรงจะค่อยๆ ลดลงอย่างช้าๆ หลังจากมีความหนาถึงระดับหนึ่ง (100μm) พื้นที่ของโพรงจะกลับด้านและเริ่มเพิ่มขึ้นตามความหนาของตาข่ายเหล็กที่เพิ่มขึ้น ดังแสดงในรูปที่ 7
นี่แสดงให้เห็นว่าเมื่อปริมาณของสารบัดกรีเพิ่มขึ้น ดีบุกของเหลวที่มีกรดไหลย้อนจะถูกชิปปกคลุมไว้ และช่องระบายอากาศที่ตกค้างจะแคบเพียงสี่ด้านเท่านั้น เมื่อปริมาณของสารบัดกรีเปลี่ยนไป ช่องระบายอากาศที่ตกค้างก็จะเพิ่มขึ้นเช่นกัน และการระเบิดของอากาศทันทีที่ห่อด้วยดีบุกเหลวหรือกระป๋องของเหลวที่ระเหยด้วยก๊าซระเหยจะทำให้ดีบุกเหลวกระเด็นไปรอบๆ QFN และชิป
การทดสอบพบว่าเมื่อความหนาของตาข่ายเหล็กเพิ่มขึ้น ฟองสบู่แตกที่เกิดจากการหลบหนีของอากาศหรือก๊าซระเหยก็จะเพิ่มขึ้นเช่นกัน และความน่าจะเป็นที่ดีบุกจะกระเด็นรอบๆ QFN และชิปก็จะเพิ่มขึ้นตามไปด้วย
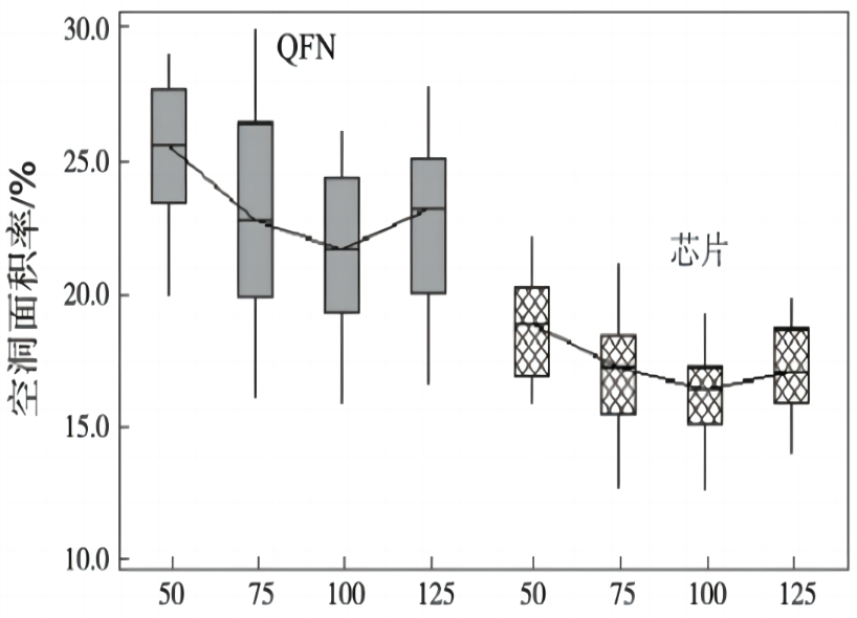
การเปรียบเทียบรูในตาข่ายเหล็กที่มีความหนาต่างกัน
3.3 อัตราส่วนพื้นที่ของช่องเชื่อมและช่องเปิดตาข่ายเหล็ก
ทดสอบตาข่ายเหล็กพิมพ์ที่มีอัตราการเปิด 100%, 90% และ 80% และเงื่อนไขอื่นๆ ยังคงไม่เปลี่ยนแปลง หลังจากการรีโฟลว์ จะมีการวัดพื้นที่โพรงของชั้นที่เชื่อมและเปรียบเทียบกับตาข่ายเหล็กที่พิมพ์ด้วยอัตราการเปิด 100% พบว่าไม่มีความแตกต่างอย่างมีนัยสำคัญในช่องของชั้นเชื่อมภายใต้เงื่อนไขอัตราการเปิด 100% และ 90% 80% ดังแสดงในรูปที่ 8
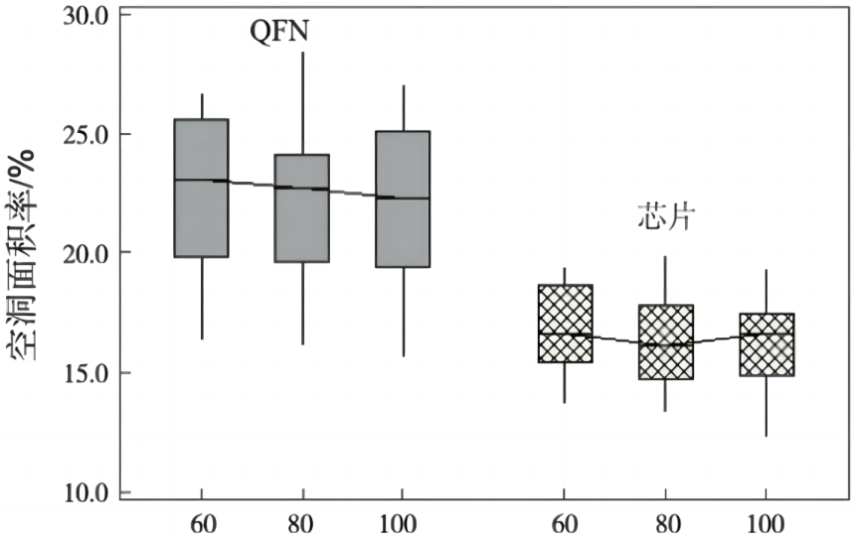
การเปรียบเทียบช่องเปิดของพื้นที่เปิดต่างๆ ของตาข่ายเหล็กต่างๆ
3.4 ช่องเชื่อมและรูปทรงตาข่ายเหล็กพิมพ์ลาย
ด้วยการทดสอบรูปร่างการพิมพ์ของสารบัดกรีของแถบ b และตารางเอียง c เงื่อนไขอื่นๆ ยังคงไม่เปลี่ยนแปลง หลังจากการรีโฟลว์ จะมีการวัดพื้นที่โพรงของชั้นการเชื่อมและเปรียบเทียบกับรูปร่างการพิมพ์ของกริด a พบว่าไม่มีความแตกต่างที่มีนัยสำคัญในช่องของชั้นเชื่อมภายใต้เงื่อนไขของตาราง แถบ และตารางเอียง ดังแสดงในรูปที่ 9
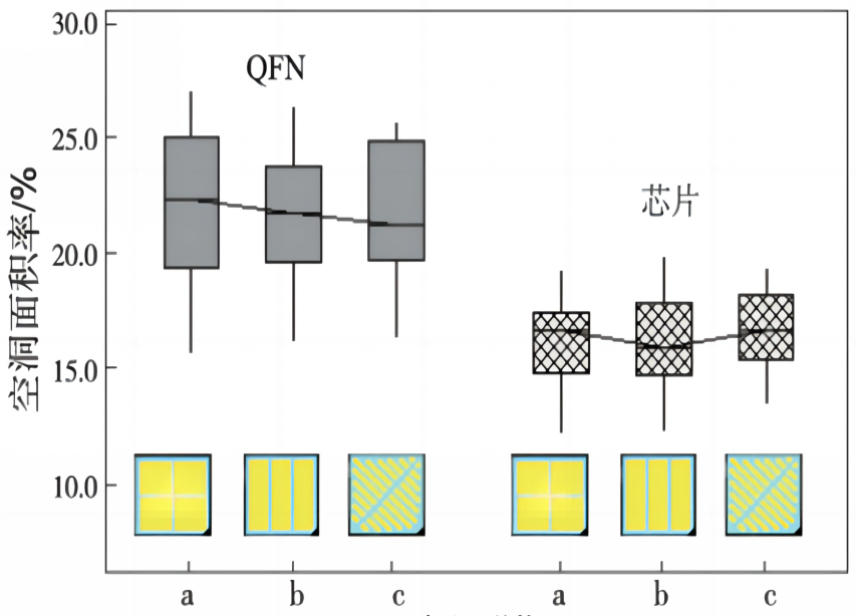
การเปรียบเทียบรูในรูปแบบการเปิดต่างๆ ของตาข่ายเหล็ก
3.5 ช่องเชื่อมและเวลาในการไหลย้อน
หลังจากทดสอบเวลาไหลย้อนเป็นเวลานาน (70 วินาที, 80 วินาที, 90 วินาที) เงื่อนไขอื่นๆ ยังคงไม่เปลี่ยนแปลง วัดรูในชั้นการเชื่อมหลังจากไหลย้อน และเมื่อเปรียบเทียบกับเวลาไหลย้อน 60 วินาที พบว่าด้วยการเพิ่มขึ้นของ เวลาไหลย้อน พื้นที่รูเชื่อมลดลง แต่แอมพลิจูดของการลดจะค่อยๆ ลดลงตามระยะเวลาที่เพิ่มขึ้น ดังแสดงในรูปที่ 10 แสดงให้เห็นว่าในกรณีที่ไม่เพียงพอ เวลาไหลย้อน การเพิ่มเวลาไหลย้อนจะเอื้อต่อการไหลล้นของอากาศที่ห่อด้วยดีบุกเหลวหลอมเหลว แต่หลังจากเวลาไหลย้อนเพิ่มขึ้นจนถึงระยะเวลาหนึ่ง อากาศที่ห่อด้วยดีบุกเหลวก็ยากที่จะล้นอีกครั้ง เวลาไหลย้อนเป็นปัจจัยหนึ่งที่ส่งผลต่อช่องเชื่อม
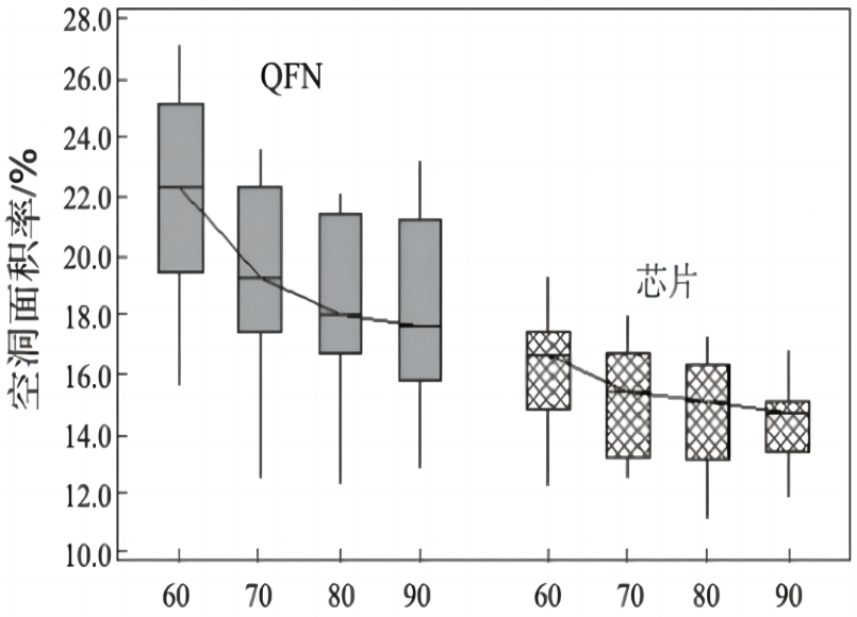
การเปรียบเทียบที่เป็นโมฆะของระยะเวลากรดไหลย้อนที่แตกต่างกัน
3.6 ช่องเชื่อมและอุณหภูมิเตาเผาสูงสุด
ด้วยการทดสอบอุณหภูมิสูงสุดของเตาเผาที่ 240 ℃ และ 250 ℃ และเงื่อนไขอื่น ๆ ไม่เปลี่ยนแปลง พื้นที่โพรงของชั้นที่เชื่อมจะถูกวัดหลังจากการรีโฟลว์ และเมื่อเปรียบเทียบกับอุณหภูมิเตาเผาสูงสุดที่ 260 ℃ พบว่าภายใต้สภาวะอุณหภูมิสูงสุดของเตาเผาที่แตกต่างกัน ช่องของ ชั้นเชื่อมของ QFN และชิปไม่มีการเปลี่ยนแปลงอย่างมีนัยสำคัญ ดังแสดงในรูปที่ 11 ซึ่งแสดงให้เห็นว่าอุณหภูมิเตาสูงสุดที่แตกต่างกันไม่มีผลกระทบที่ชัดเจนต่อ QFN และรูในชั้นการเชื่อมของชิป ซึ่งก็คือ ไม่ใช่ปัจจัยที่มีอิทธิพล
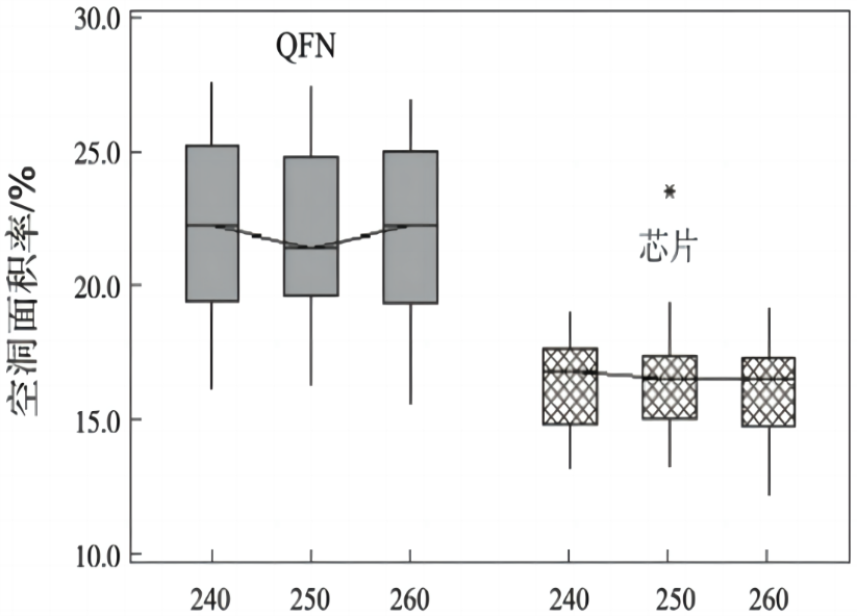
การเปรียบเทียบอุณหภูมิสูงสุดที่แตกต่างกันเป็นโมฆะ
การทดสอบข้างต้นบ่งชี้ว่าปัจจัยสำคัญที่ส่งผลต่อช่องชั้นเชื่อมของ QFN และชิปคือเวลาไหลย้อนและความหนาของตาข่ายเหล็ก
4 การปรับปรุงช่องเชื่อม reflow การพิมพ์แบบวางประสาน
4.1การทดสอบ DOE เพื่อปรับปรุงช่องเชื่อม
รูในชั้นการเชื่อมของ QFN และชิปได้รับการปรับปรุงให้ดีขึ้นโดยการค้นหาค่าที่เหมาะสมที่สุดของปัจจัยที่มีอิทธิพลหลัก (เวลาไหลย้อนและความหนาของตาข่ายเหล็ก) เนื้อบัดกรีคือ SAC305 type4 รูปร่างตาข่ายเหล็กเป็นแบบกริด (องศาเปิด 100%) อุณหภูมิเตาสูงสุดคือ 260 ℃ และเงื่อนไขการทดสอบอื่น ๆ ก็เหมือนกับอุปกรณ์ทดสอบ การทดสอบ DOE และผลลัพธ์แสดงไว้ในตารางที่ 3 อิทธิพลของความหนาของตาข่ายเหล็กและเวลาการไหลย้อนต่อ QFN และรูเชื่อมชิปแสดงในรูปที่ 12 จากการวิเคราะห์ปฏิกิริยาของปัจจัยที่มีอิทธิพลหลัก พบว่าการใช้ความหนาของตาข่ายเหล็ก 100 μm และเวลาไหลย้อน 80 วินาทีสามารถลดช่องเชื่อมของ QFN และชิปได้อย่างมาก อัตราช่องเชื่อมของ QFN ลดลงจากสูงสุด 27.8% เป็น 16.1% และอัตราช่องเชื่อมของชิปลดลงจากสูงสุด 20.5% เป็น 14.5%
ในการทดสอบ มีการผลิตผลิตภัณฑ์ 1,000 รายการภายใต้สภาวะที่เหมาะสม (ความหนาของตาข่ายเหล็ก 100 μm เวลาไหลย้อน 80 วินาที) และสุ่มวัดอัตราช่องเชื่อม 100 QFN และชิป อัตราช่องเชื่อมเฉลี่ยของ QFN อยู่ที่ 16.4% และอัตราช่องเชื่อมเฉลี่ยของชิปอยู่ที่ 14.7% อัตราช่องเชื่อมของชิปและชิปลดลงอย่างเห็นได้ชัด
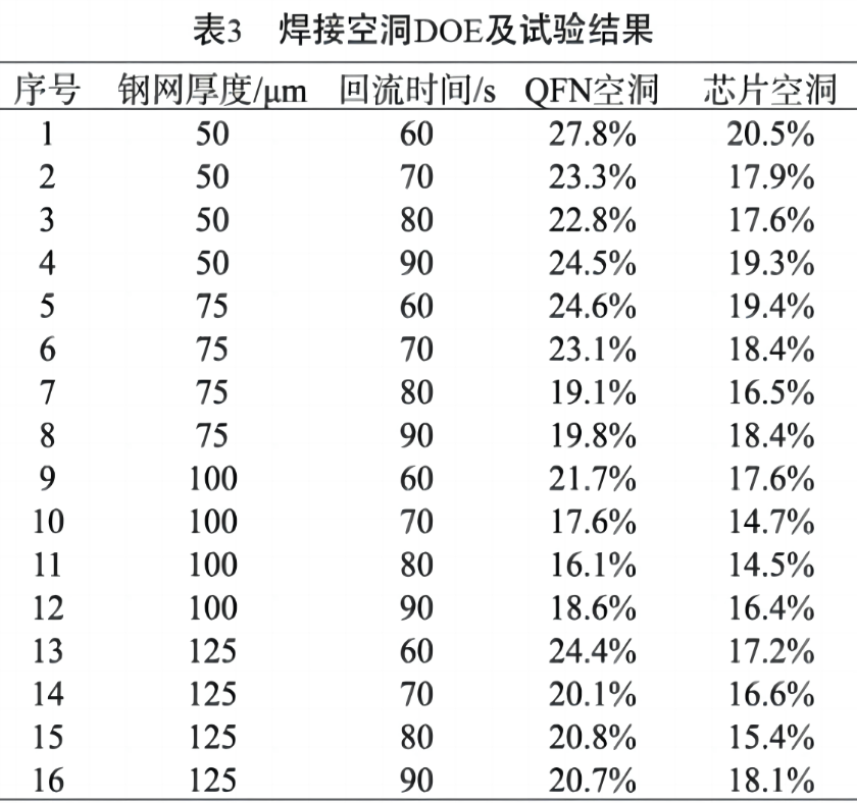
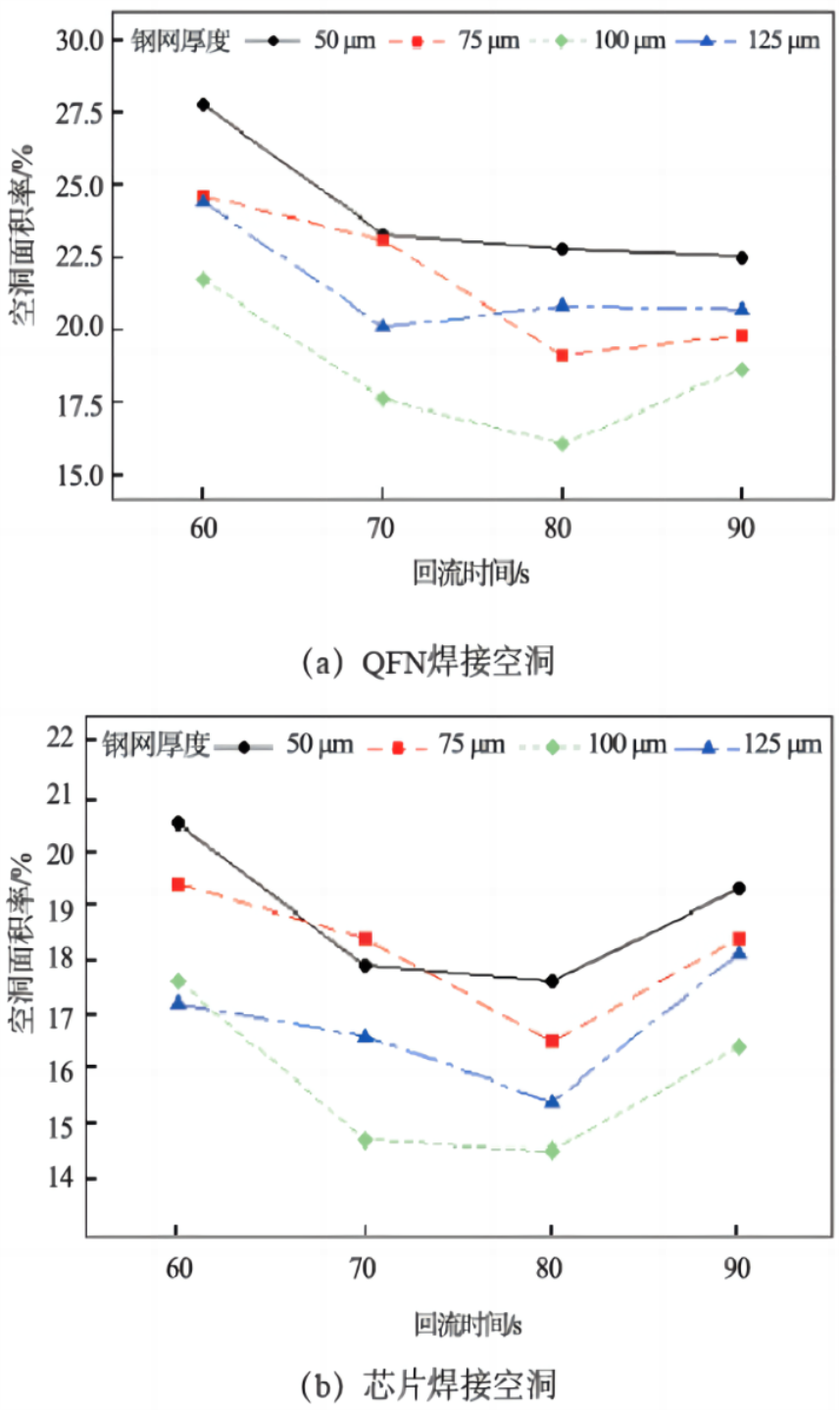
4.2 กระบวนการใหม่ปรับปรุงช่องเชื่อม
สถานการณ์การผลิตจริงและการทดสอบแสดงให้เห็นว่าเมื่อพื้นที่ช่องเชื่อมที่ด้านล่างของชิปน้อยกว่า 10% ปัญหาการแตกร้าวของตำแหน่งช่องชิปจะไม่เกิดขึ้นในระหว่างการติดตะกั่วและการขึ้นรูป พารามิเตอร์กระบวนการที่ปรับให้เหมาะสมโดย DOE ไม่สามารถตอบสนองข้อกำหนดในการวิเคราะห์และแก้ไขรูในการเชื่อมแบบรีโฟลว์แบบบัดกรีแบบธรรมดา และต้องลดอัตราพื้นที่ช่องเชื่อมของชิปลงอีก
เนื่องจากชิปที่หุ้มอยู่บนตัวบัดกรีจะป้องกันไม่ให้ก๊าซในตัวบัดกรีหลุดออกไป อัตรารูที่ด้านล่างของชิปจึงลดลงอีกโดยการกำจัดหรือลดก๊าซที่เคลือบด้วยโลหะบัดกรี กระบวนการใหม่ของการเชื่อมแบบรีโฟลว์ด้วยการพิมพ์แบบวางบัดกรีสองแบบถูกนำมาใช้: การพิมพ์แบบวางแบบบัดกรีหนึ่งแบบ, แบบรีโฟลว์หนึ่งครั้งที่ไม่ครอบคลุม QFN และชิปเปล่าที่ปล่อยก๊าซในบัดกรี กระบวนการเฉพาะของการพิมพ์แบบวางบัดกรีรอง แพทช์ และการไหลย้อนทุติยภูมิจะแสดงในรูปที่ 13
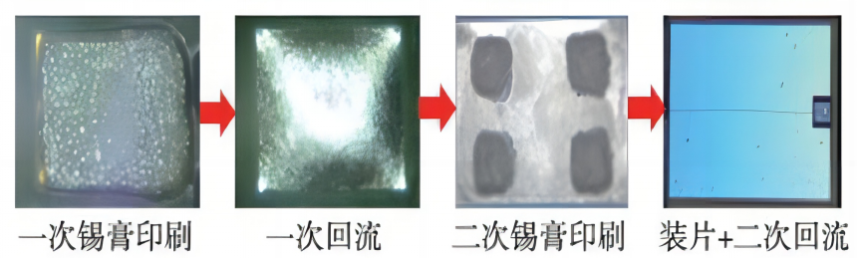
เมื่อพิมพ์สารบัดกรีที่มีความหนา 75μm เป็นครั้งแรก ก๊าซส่วนใหญ่ในการบัดกรีที่ไม่มีฝาปิดชิปจะหลุดออกจากพื้นผิว และความหนาหลังจากกรดไหลย้อนจะอยู่ที่ประมาณ 50μm หลังจากเสร็จสิ้นการไหลย้อนเบื้องต้น จะมีการพิมพ์สี่เหลี่ยมเล็กๆ บนพื้นผิวของโลหะบัดกรีที่แข็งตัวด้วยความเย็น (เพื่อลดปริมาณของโลหะบัดกรี ลดปริมาณของก๊าซที่หกรั่วไหล ลดหรือกำจัดการกระเด็นของโลหะบัดกรี) และโลหะบัดกรีด้วย ความหนา 50 μm (ผลการทดสอบข้างต้นแสดงว่า 100 μm ดีที่สุด ดังนั้นความหนาของการพิมพ์รองคือ 100 μm.50 μm=50 μm) จากนั้นทำการติดตั้ง ชิปแล้วย้อนกลับผ่าน 80 วินาที แทบไม่มีรูในการบัดกรีหลังจากการพิมพ์ครั้งแรกและการรีโฟลว์ และการบัดกรีในการพิมพ์ครั้งที่สองมีขนาดเล็กและรูเชื่อมมีขนาดเล็ก ดังแสดงในรูปที่ 14
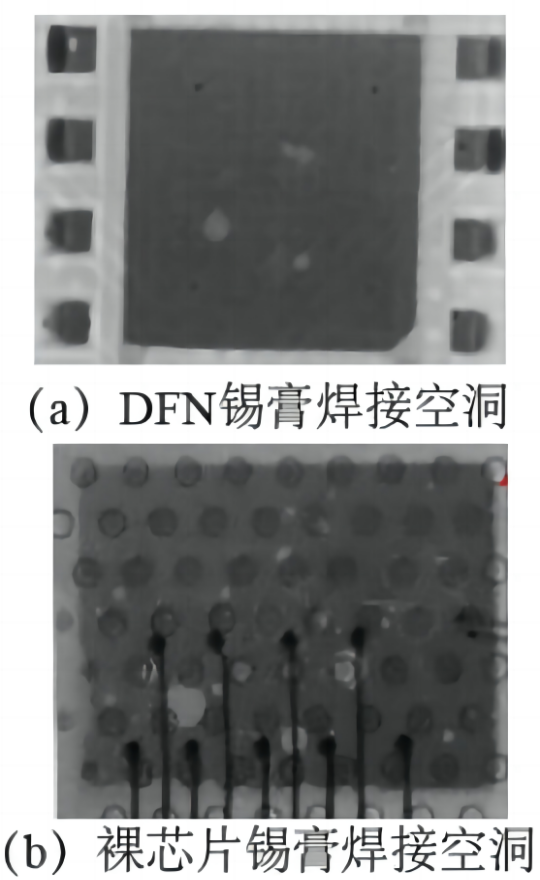
หลังจากพิมพ์บัดกรีแล้วสองครั้ง การวาดแบบกลวง
4.3 การตรวจสอบผลกระทบของช่องเชื่อม
การผลิตผลิตภัณฑ์ 2,000 รายการ (ความหนาของตาข่ายเหล็กการพิมพ์ครั้งแรกคือ 75 μm ความหนาของตาข่ายเหล็กการพิมพ์ครั้งที่สองคือ 50 μm) เงื่อนไขอื่น ๆ ไม่เปลี่ยนแปลง การวัดแบบสุ่ม 500 QFN และอัตราช่องเชื่อมชิป พบว่ากระบวนการใหม่ หลังจากการไหลย้อนครั้งแรกไม่มีช่อง หลังจากการไหลย้อนครั้งที่สอง QFN อัตราช่องเชื่อมสูงสุดคือ 4.8% และอัตราช่องเชื่อมสูงสุดของชิปคือ 4.1% เมื่อเปรียบเทียบกับกระบวนการเชื่อมด้วยการพิมพ์แบบวางครั้งเดียวแบบเดิมและกระบวนการที่ได้รับการปรับปรุง DOE แล้ว ช่องการเชื่อมจะลดลงอย่างมาก ดังแสดงในรูปที่ 15 ไม่พบรอยแตกร้าวของเศษหลังจากการทดสอบการทำงานของผลิตภัณฑ์ทั้งหมด
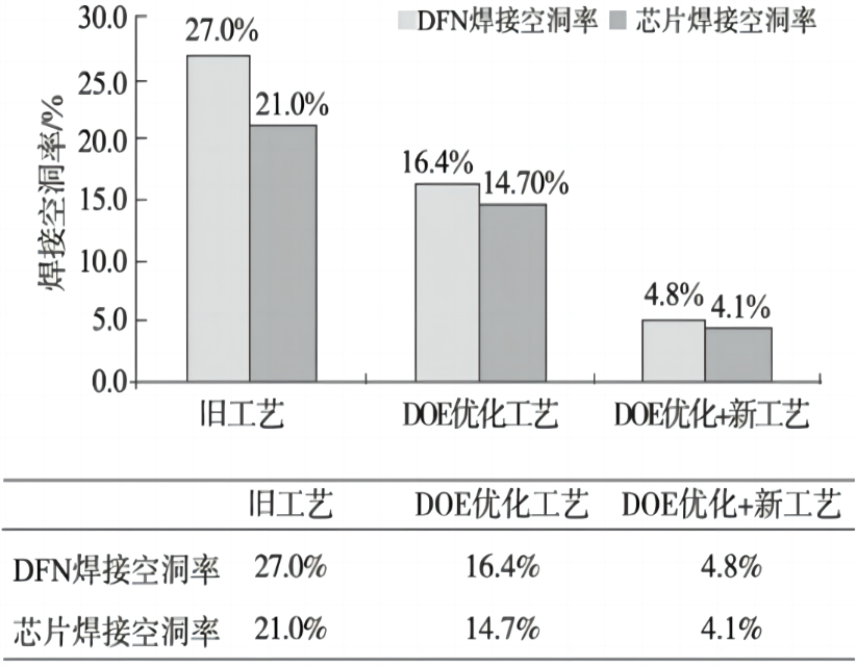
5 สรุป
การเพิ่มประสิทธิภาพของจำนวนการพิมพ์แบบวางประสานและเวลาในการไหลย้อนสามารถลดพื้นที่ของช่องเชื่อมได้ แต่อัตราของช่องเชื่อมยังคงมีขนาดใหญ่ การใช้เทคนิคการเชื่อมแบบรีโฟลว์การพิมพ์แบบวางประสานสองแบบสามารถเพิ่มประสิทธิภาพและเพิ่มอัตราช่องเชื่อมได้อย่างมีประสิทธิภาพ พื้นที่การเชื่อมของชิปเปลือยวงจร QFN สามารถมีขนาด 4.4 มม. x 4.1 มม. และ 3.0 มม. x 2.3 มม. ตามลำดับในการผลิตจำนวนมาก อัตราโพรงของการเชื่อมแบบรีโฟลว์ถูกควบคุมต่ำกว่า 5% ซึ่งช่วยปรับปรุงคุณภาพและความน่าเชื่อถือของการเชื่อมแบบรีโฟลว์ การวิจัยในบทความนี้เป็นข้อมูลอ้างอิงที่สำคัญในการปรับปรุงปัญหาช่องเชื่อมของพื้นผิวการเชื่อมพื้นที่ขนาดใหญ่
เวลาโพสต์: Jul-05-2023